Types of Injection Molding Machine : Choose Hydraulic, Electric or Hybrid Wisely
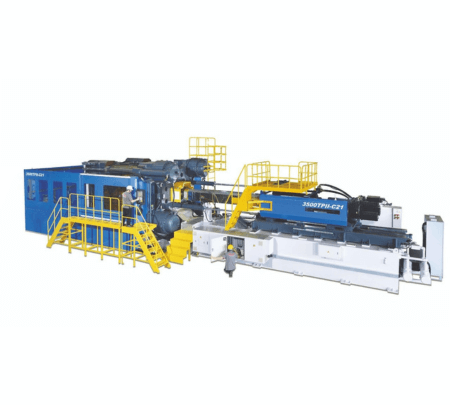
Choosing wisely among hydraulic, electric, and hybrid injection molding machines is the first step toward maximizing production efficiency, product quality, and long-term ROI. While the three drive systems share the same basic molding cycle, each combines power, precision, energy demand, and maintenance requirements in a different way. By weighing these trade-offs up front, manufacturers can align machine capabilities with their part geometry, sustainability targets, and budget—and avoid costly missteps down the road.
What Is an Injection Molding Machine?
An injection molding machine melts plastic pellets, injects the molten resin into a closed mold, then cools and ejects the finished part—repeating this cycle thousands of times with high precision. It consists of two primary units: the injection unit (plasticizing & dosing) and the clamping unit (closing, holding, and opening the mold).
Why Selecting the Right Type Matters
Selecting the right injection molding machine involves considering several key factors:
- Production Volume & Part Size
- Precision & Repeatability Requirements
- Energy Consumption / ESG Goals
- Budget (Cap-Ex) vs. Long-Term Operational Cost (Op-Ex)
- Maintenance, Uptime & Serviceability
Three Main Types of Injection Molding Machines
-
Hydraulic Injection Molding Machines
Hydraulic injection molding machines have been a staple in the industry for decades due to their robust design and versatility. Hydraulic machines use hydraulic cylinders to generate the necessary force for molding operations. This technology has evolved to offer enhanced performance and reliability.
Typical tonnage range: 100 – 4,000 t, making hydraulics ideal for large-part production.
Advantages:
- High clamping force for large and complex parts
- Lower initial cost
- Easy to maintain and operate
Disadvantages:
- Higher energy consumption
- Potential for oil leaks and slower cycle times
Industry Applications
Hydraulic machines are best suited for heavy-duty applications and the production of larger parts, such as automotive components, plastic pallets and large household items.
Looking for a hydraulic injection molding machine? Explore the Two-Platen Injection Molding Machine - CLF TWII series. -
Electric Injection Molding Machines
Electric injection molding machines have gained popularity for their precision and efficiency. Electric machines use electric servo motors to drive the molding process, offering superior control and repeatability.
Energy-saving potential: up to 70 % lower electricity consumption than comparable hydraulic models.
Advantages:
- Superior energy efficiency
- High precision and repeatability
- Cleanroom-compatible (no hydraulic oil)
Disadvantages:
- Higher initial investment
- Limited clamping force for very large parts
Industry Applications
Electric machines are ideal for high-precision and clean-room applications, such as medical devices and electronic components.
Looking for an electric injection molding machine? Contact us for customized service. -
Hybrid Injection Molding Machines
Hybrid injection molding machines combine the best of both hydraulic and electric technologies to offer a balanced solution. Hybrid machines use a combination of hydraulic and electric systems to provide both high precision and strong clamping force.
Real-world result : one CLF automotive client boosted output 25 % while cutting energy 30 % after switching to hybrids.
Advantages:
- Energy savings with high clamping power
- Flexible for various production types
Disadvantages:
- More complex to maintain
- Medium initial cost
Industry Applications
Hybrid machines are suitable for applications requiring a balance of precision and power, such as automotive parts and consumer goods.
Ready for hybrid versatility? Talk with our team today.
Key Factors to Consider When Choosing a Machine
-
Part Size & Complexity : Estimate the required tonnage (clamping force) using part area and material type. A widely used estimation formula is:
Tonnage (tons) = Projected Area (in²) × Clamp Factor (typically 3–8 tons/in²)
This formula originates from practical industry experience. The projected area represents the surface area of the part facing the mold’s parting line. The clamp factor varies based on material viscosity and part geometry: lower for thin, free-flowing parts and higher for thick or fiber-reinforced parts. This ensures enough clamping force is applied to prevent flash during injection.
Read our full guide on how the tonnage formula works and how to apply it correctly (clamping force) using part area and material type - Material Used: Thermoplastics, thermosets, silicone, or metal powders
- Production Volume: Electric for high-speed precision, hydraulic for high-tonnage needs
- Energy Efficiency: Electric and hybrid machines offer long-term savings
- Cleanroom Compliance: Go electric or LSR for sterile manufacturing environments
- Maintenance & Reliability: Electric machines offer lower downtime; hybrid machines need expert maintenance
Common Injection Molding Machine Configurations & Options
Beyond machine types, specific configurations and functional enhancements also influence injection molding efficiency and machine suitability:
-
Quick Mold Change (QMC) Systems: QMC technology significantly improves production efficiency by reducing mold changeover time, especially in high-mix, low-volume environments. When paired with automation and smart scheduling, QMC minimizes downtime and boosts flexibility in operations.
Learn more about how QMC and automation drive injection molding efficiency - Servo Motor Systems: Improve energy savings and precision control in injection, clamping, and ejector stages—widely used in electric and hybrid machines.
- Automation Integration: Compatibility with robots, conveyors, and in-mold labeling systems enhances productivity and consistency.
- Smart Control Panels: Industry 4.0-ready HMIs allow real-time data logging, predictive maintenance, and remote troubleshooting.
Injection Molding Machine Comparison Table
Feature | Hydraulic | Electric | Hybrid |
---|---|---|---|
Clamping Force | High | Medium | High |
Energy Consumption | High | Low | Medium |
Initial Investment | Low | High | Medium |
Precision | Medium | High | High |
Maintenance | Moderate | Low | Moderate to High |
Cycle Time / Speed | Slower | Fast | Moderate |
Ideal Applications | Large parts | Precision, medical | Versatile |
Key Factors That Influence Pricing
The cost of an injection molding machine depends on several critical factors, including clamping force, drive system, machine configuration, and automation capabilities. While prices vary widely across regions and applications, manufacturers are encouraged to look beyond initial investment and focus on total cost of ownership —which includes energy efficiency, maintenance needs, productivity, and lifecycle support.
Key factors that influence pricing :
- Clamping force & machine size : Higher tonnage machines naturally command a higher investment due to structural and hydraulic requirements.
- Drive system : Electric machines generally cost more upfront but deliver long-term savings through energy efficiency and precision.
- Automation & smart features : Machines integrated with servo motors, Industry 4.0-ready HMIs, and robotic systems typically fall into premium tiers.
- Brand reputation & support : Trusted brands with global service networks and advanced customization options often reflect that value in their pricing structure.
While CLF offers competitive and customizable solutions across hydraulic, hybrid, and electric platforms, the right machine is the one that aligns with your production goals, material choices, and operational budget.
Finding the Right Fit for Your Needs
Choosing the best injection molding machine depends on your specific production goals, material requirements, and cost considerations.
- Go hydraulic for affordability and power
- Choose electric for precision and energy savings
- Opt for hybrid for a balance of both worlds
- Consider specialty machines for unique materials or configurations
Market Trends: What's Shaping Injection Molding Machines in 2025
The injection molding machine market is being shaped by four major trends: rising demand in Asia-Pacific, a global push for sustainability and recycling, smart manufacturing technologies like AI and IoT, and increased use of large-tonnage machines for industrial packaging and logistics. These trends are influencing purchasing decisions and product development across the industry.
Read the full article : 4 Key Trends Shaping the Future of Injection Molding Machines in 2025
About CLF: Taiwan’s Injection Molding Machine Pioneer
Founded in 1966, CLF is a leading Taiwanese manufacturer of injection molding machines with more than five decades of experience. With a global customer base and a reputation for innovation, CLF specializes in producing hydraulic, hybrid, and electric injection molding machines that serve industries ranging from automotive and consumer goods to electronics and packaging.
Key Services & Capabilities:
- Customizable machine configurations (50 to 4000+ tons)
- Energy-saving servo system solutions
- Turnkey production support and after-sales service
- International certifications and smart manufacturing integrations
Customer Success Case: A major Southeast Asian packaging company partnered with CLF to upgrade its production line with high-tonnage TWII-series hydraulic machines. The result? A 25% increase in output capacity, 30% energy savings, and smoother operation with CLF's intelligent monitoring system.
Whether you are launching a new production line or upgrading your current setup, CLF is your trusted partner in achieving long-term success through high-performance injection molding solutions.
Ready to Find the Right Injection Molding Machine?
If you're looking for a reliable and experienced partner in injection molding, CLF is here to help. From personalized consultations to full turnkey production support, our team is committed to delivering the best-fit solution for your manufacturing needs.
Contact our experts today and take the first step toward optimized production with CLF.