The Ultimate Guide to Plastic Cap Manufacturing : Materials, Processes and Innovations
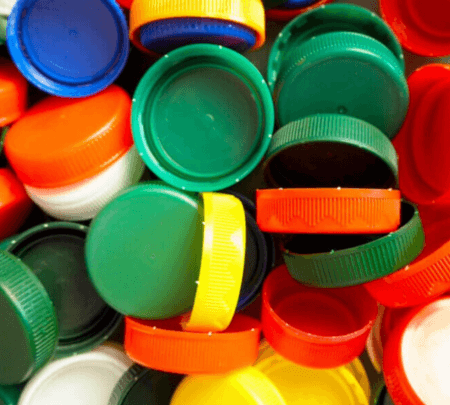
Plastic caps play a vital role in packaging across industries such as food and beverage, pharmaceuticals, and cosmetics. Their production has evolved significantly, with advancements in materials, manufacturing techniques, and sustainability efforts. As demand for lightweight, durable, and recyclable caps grows, manufacturers are adopting innovative processes to improve efficiency and reduce environmental impact. This guide explores the key aspects of plastic cap manufacturing, including :
- Types of plastic caps and their applications
- Material selection and its impact on sustainability
- Manufacturing processes
- Latest innovations in plastic cap production
- Future trends : AI, automation, and sustainability regulations
Types of Plastic Caps and Their Applications
Plastic caps are industry-specific, designed to ensure product protection, user-friendly design, and compliance with safety standards. Each design serves specific functions for various industries.
Common Plastic Cap Types :
- Screw Caps : Ideal for beverages, household cleaning products, and pharmaceuticals, ensuring a hermetic seal.
- Flip-Top Caps : Used in personal care and food products, providing convenient dispensing.
- Snap-Fit Caps : Common in dairy and pharmaceutical packaging, designed for ease of use.
- Child-Resistant Caps : Essential in pharmaceuticals and chemical packaging to prevent accidental ingestion.
- Tamper-Evident Caps : Provides visible security features in the food and beverage industries.
- Dispensing Caps : Including trigger sprayers, pumps, and droppers, widely used in cosmetics and healthcare.
Choosing the right cap design ensures product safety, reinforces brand identity, and supports sustainability efforts. Child-resistant caps enhance safety in pharmaceuticals, while tamper-evident caps ensure integrity in food and beverage packaging. Flip-top and dispensing caps improve user convenience, and lightweight, recyclable caps help brands meet sustainability goals without compromising functionality.
Plastic caps are essential in various industries, ensuring secure sealing, user-friendly design, product safety, and functionality tailored to specific industry requirements for beverage bottles, pharmaceutical containers, and personal care products. To learn more about their applications and sustainability impact, visit our Packaging Applications.
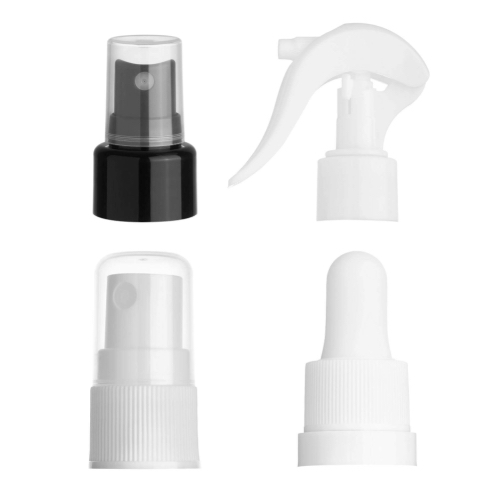
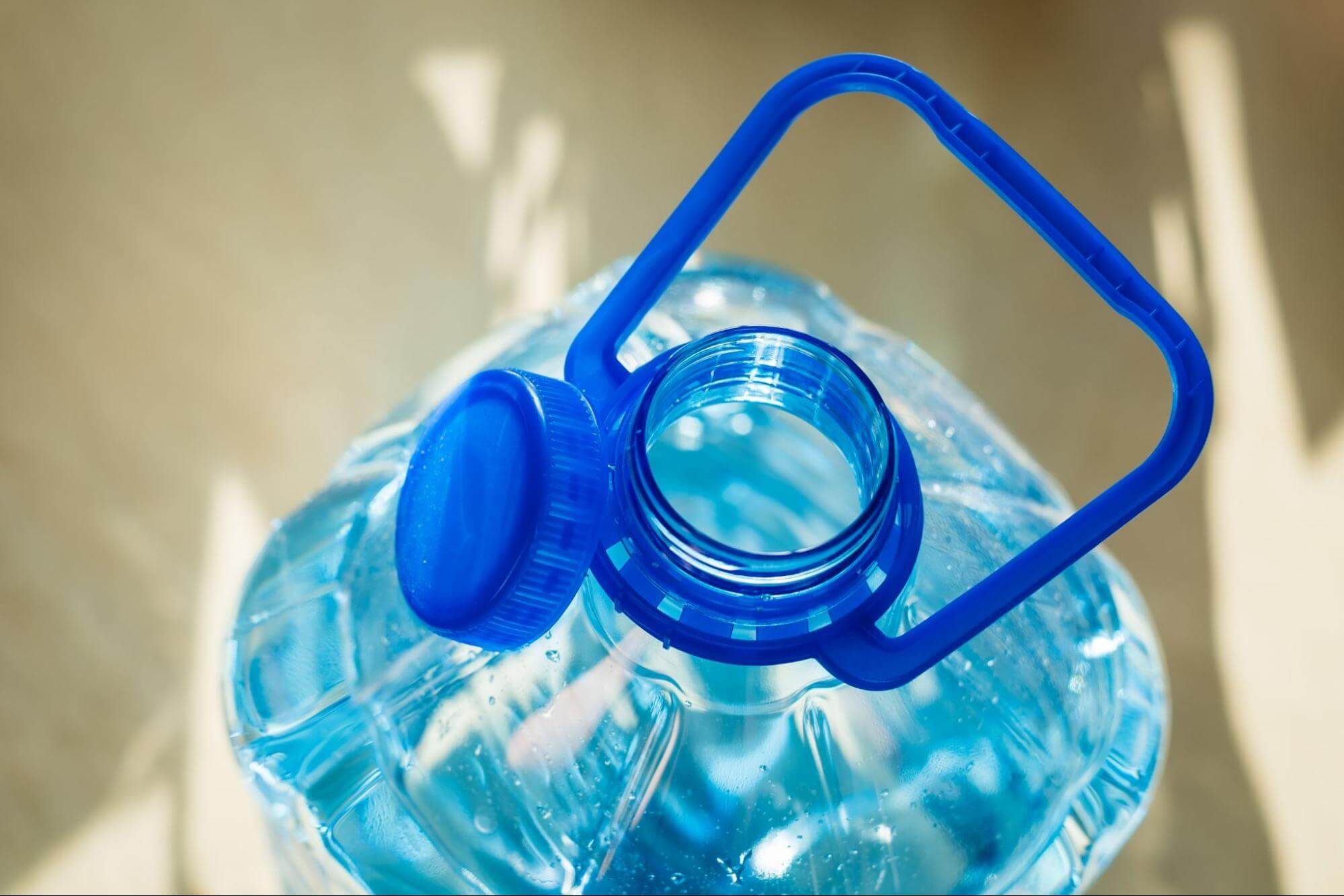
Materials Used in Plastic Cap Manufacturing
Selecting the right material impacts cap strength, recyclability, and functionality.
- Polypropylene (PP) : The most common material, offering lightweight strength and recyclability.
- High-Density Polyethylene (HDPE) : Impact-resistant and widely used in beverage and chemical packaging.
- Low-Density Polyethylene (LDPE) : Flexible and soft, ideal for squeeze bottle caps.
- Recycled & Bio-Based Plastics : Growing demand for PCR (post-consumer recycled) materials and biodegradable plastics.
Modern injection molding machines are now optimized to process sustainable materials by incorporating advanced heating and cooling systems, precision dosing technology, and energy-efficient servo motors. These enhancements reduce energy consumption, minimize material waste, and improve production efficiency while maintaining high-quality output.
Key Manufacturing Process : Injection Molding
Injection molding is the primary method for plastic cap production due to its speed, precision, and cost-effectiveness.
Injection Molding Process for Plastic Caps
- Material Selection : Thermoplastic resins like PP (polypropylene) or HDPE (high-density polyethylene) are chosen for durability and flexibility.
- Melting & Injection : Plastic is melted and injected into a custom-designed mold under high pressure.
- Cooling & Solidification : The mold cools the plastic, forming the cap’s shape.
- Ejection & Finishing : The cap is released and undergoes post-processing, such as deburring and quality inspection.
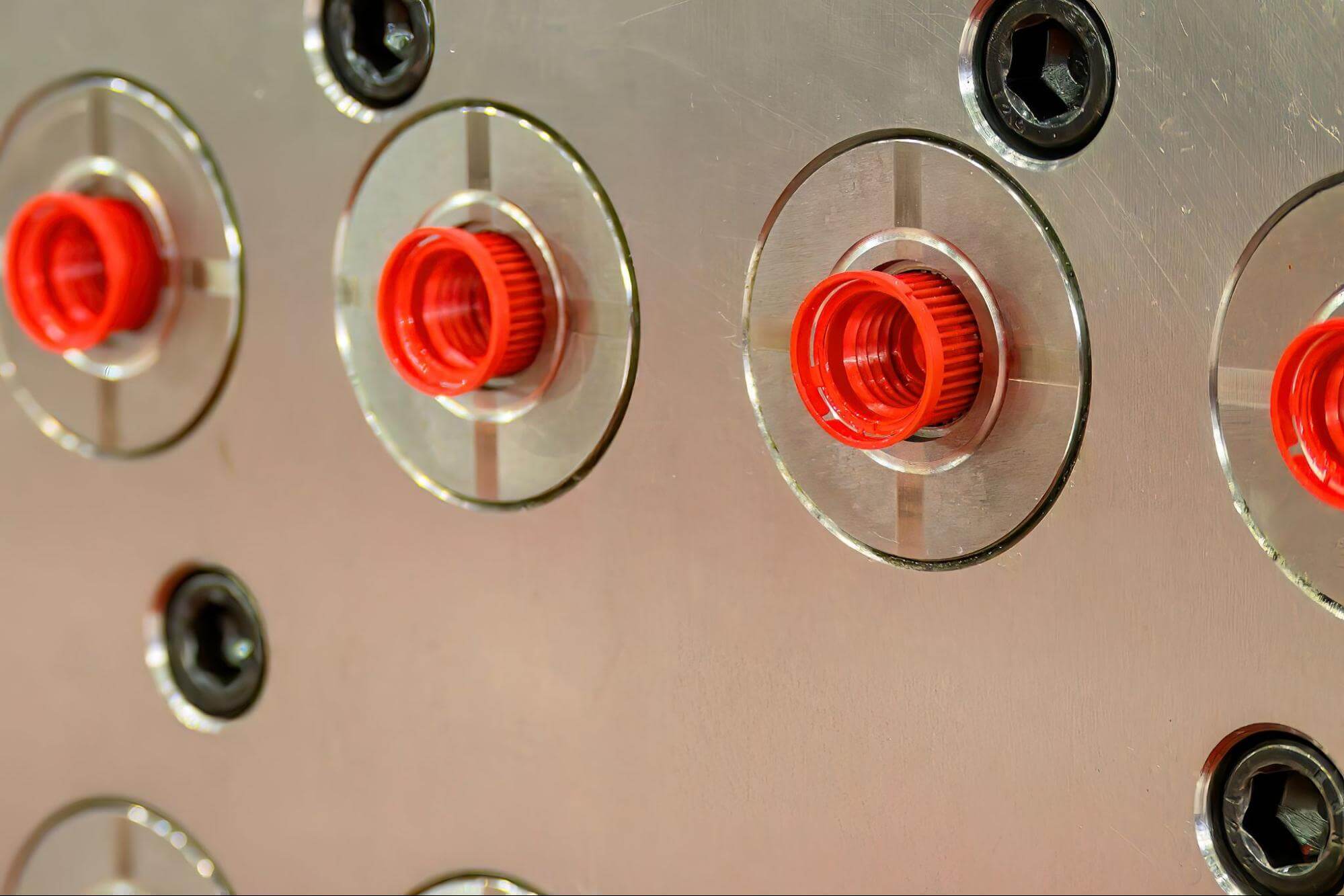
Advantages of Injection Molding in Plastic Cap Manufacturing
- High-Speed Production : Efficient for large-scale manufacturing.
- Consistent Quality : Ensures uniform shape, size, and durability.
- Material Efficiency : Minimizes waste, with options for recycled plastics.
- Design Flexibility : Supports complex cap designs, including embossed logos and textured finishes.
Challenges in Injection Molding for Caps
- Precision Mold Maintenance : High-quality molds require frequent maintenance.
- Cycle Time Optimization : Faster cooling techniques are needed for high-volume production.
- Material Cost Considerations : Using sustainable or bio-based plastics can impact costs.
Innovations in Plastic Cap Manufacturing
Sustainability and technology are shaping the future of cap production.
- Lightweight Cap Design : Reducing plastic use while maintaining strength.
- Smart Caps : Featuring QR codes, NFC chips, or tamper-detection indicators for authentication.
- Eco-Friendly Materials : Using plant-based bioplastics and fully recyclable caps.
- Advanced Molding Techniques : Improving efficiency through multi-cavity molds and high-speed automation.
Future Trends in Plastic Cap Manufacturing
- Increased Sustainability Regulations : Push for fully recyclable caps and biodegradable options.
- AI-Driven Automation : Enhancing efficiency in quality inspection and defect detection.
- Customization & Branding : More companies opting for unique cap textures, colors, and embossing.
- Energy-Efficient Manufacturing : Investing in low-energy injection molding machines to cut costs and emissions.
The Role of Injection Molding Machines in Plastic Cap Production
Injection molding is the primary manufacturing method for plastic caps, ensuring :
- High precision and repeatability.
- Optimized energy efficiency through electric and hybrid models.
- Efficient production of complex designs, including tamper-evident and child-resistant caps.
CLF offers industry-leading injection molding solutions, including :
- The TX Series Standard Plastic Injection Molding Machine—featuring a five-point internal toggle mechanism for high-speed operation and a high-strength toggle configuration for durability.
- The TWR/TPIIR Series Rotary Table/Separated Injection Multi-Color Plastic Injection Molding Machine—providing greater design flexibility, cost reduction through co-injection(multiple materials injected into the same mold), and precise rotation capabilities.
Choosing the right machine ensures manufacturers meet production demands with high-quality and sustainable practices. The TX Series enhances efficiency with its five-point toggle mechanism, while the TWR/TPIIR Series enables greater design flexibility and cost savings through co-injection technology.
![]() |
![]() |
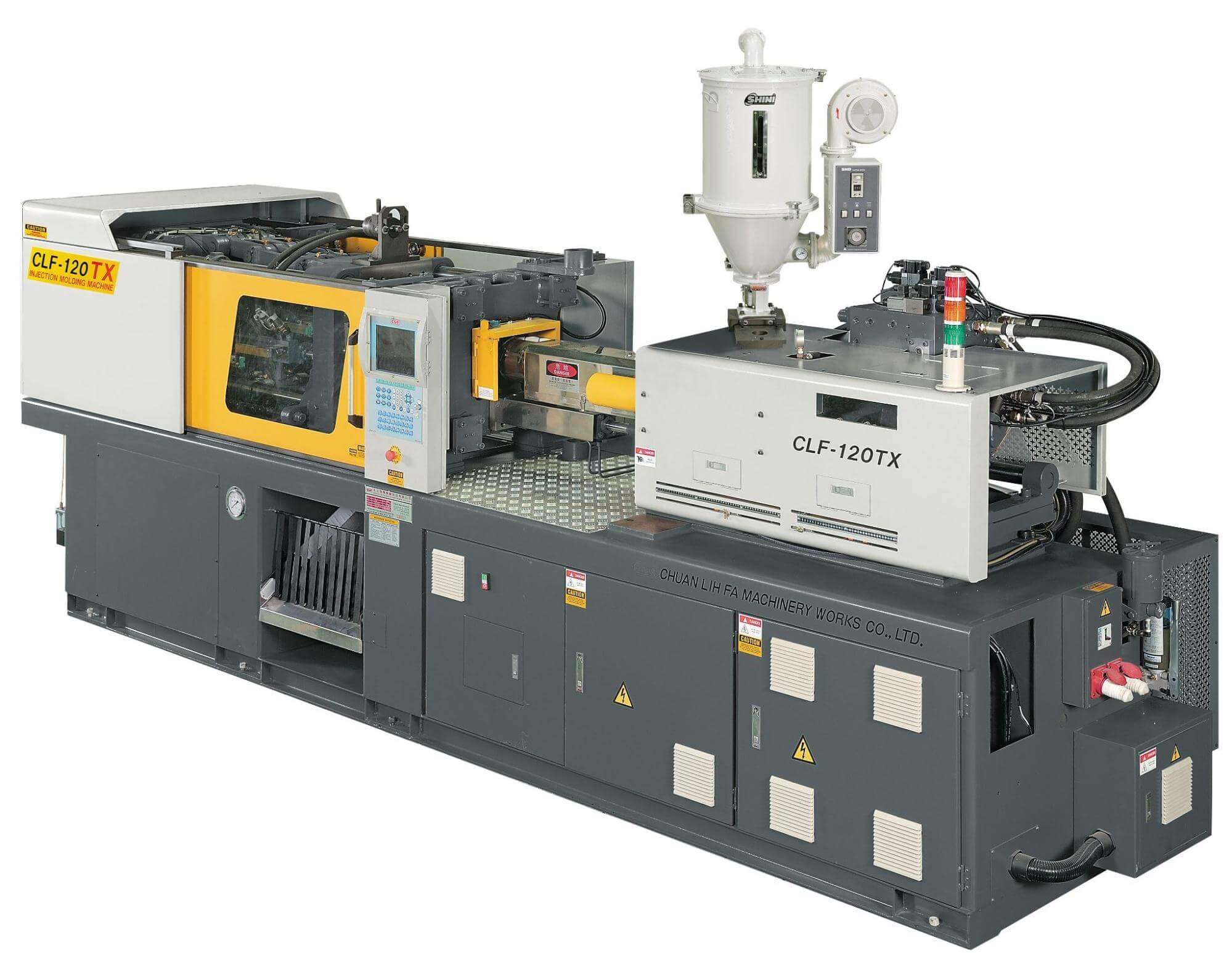
Download Catalogue for More TX Series Injection Molding Machines for Caps
The Future of Plastic Cap Manufacturing
Plastic cap manufacturing is evolving with advancements in materials, sustainability, and automation. Injection molding remains at the forefront, offering the highest level of efficiency, precision, and design flexibility.
As brands focus on lighter, smarter, and eco-friendly solutions, manufacturers must adapt by investing in
cutting-edge injection molding machines and sustainable materials.
Looking to optimize your plastic cap production? Contact CLF
today for high-performance injection molding solutions.