How Sustainability is Transforming Plastic Cap Design and Production
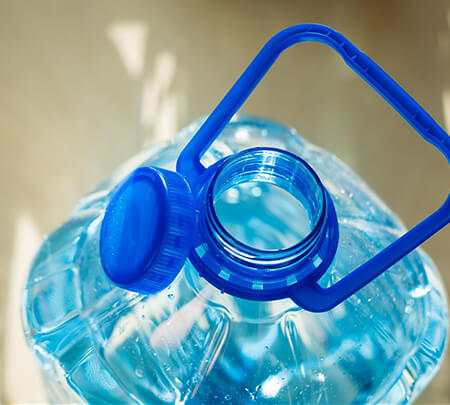
Sustainability is transforming plastic cap manufacturing as brands embrace eco-friendly materials, efficient production, and responsible sourcing. Advances in plastic cap injection molding machines enhance energy efficiency and material optimization, reducing waste and improving recyclability. This article explores key innovations in design, manufacturing, and industry trends shaping greener cap production.
1. Sustainable Design Innovations in Plastic Caps
Recyclability and Monomaterial Solutions
Recyclability is now a core principle in cap design. Manufacturers are shifting towards monomaterial caps, primarily using polypropylene (PP) or polyethylene terephthalate (PET), to enhance recyclability and improve the quality of recycled materials.
Examples :
- Heinz launched a fully recyclable ketchup cap made from PP, eliminating the silicone valve that previously complicated recycling.
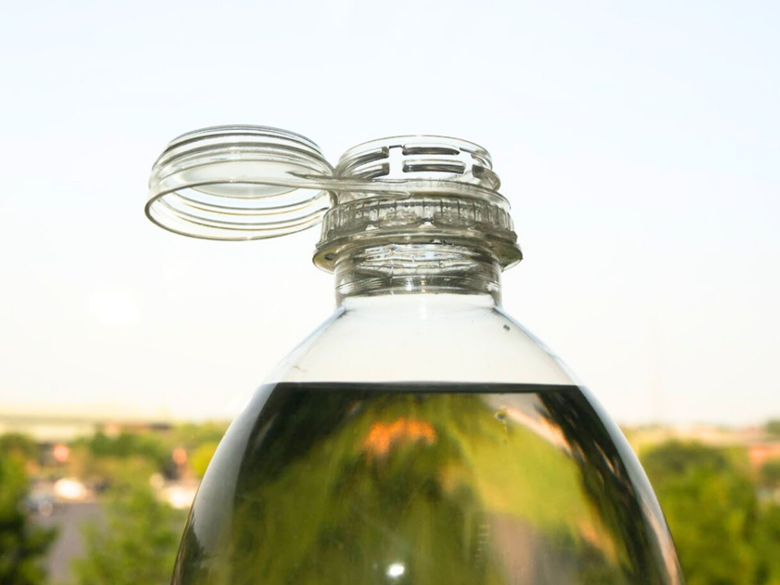
(Photo from Packaging Euro / Origin Materials announces ‘first’ tethered PET caps)
Lightweighting for Reduced Carbon Footprint
Manufacturers are actively designing lighter caps that require less plastic without compromising strength or functionality. This innovation not only lowers material costs but also reduces carbon emissions during transportation, contributing to more sustainable packaging.
Tethered Caps for Improved Recycling
Tethered caps, which remain attached to bottles after opening, are gaining popularity to reduce litter and enhance recyclability. Even without regulatory mandates, many beverage brands are proactively adopting tethered solutions to align with sustainability goals and consumer expectations.
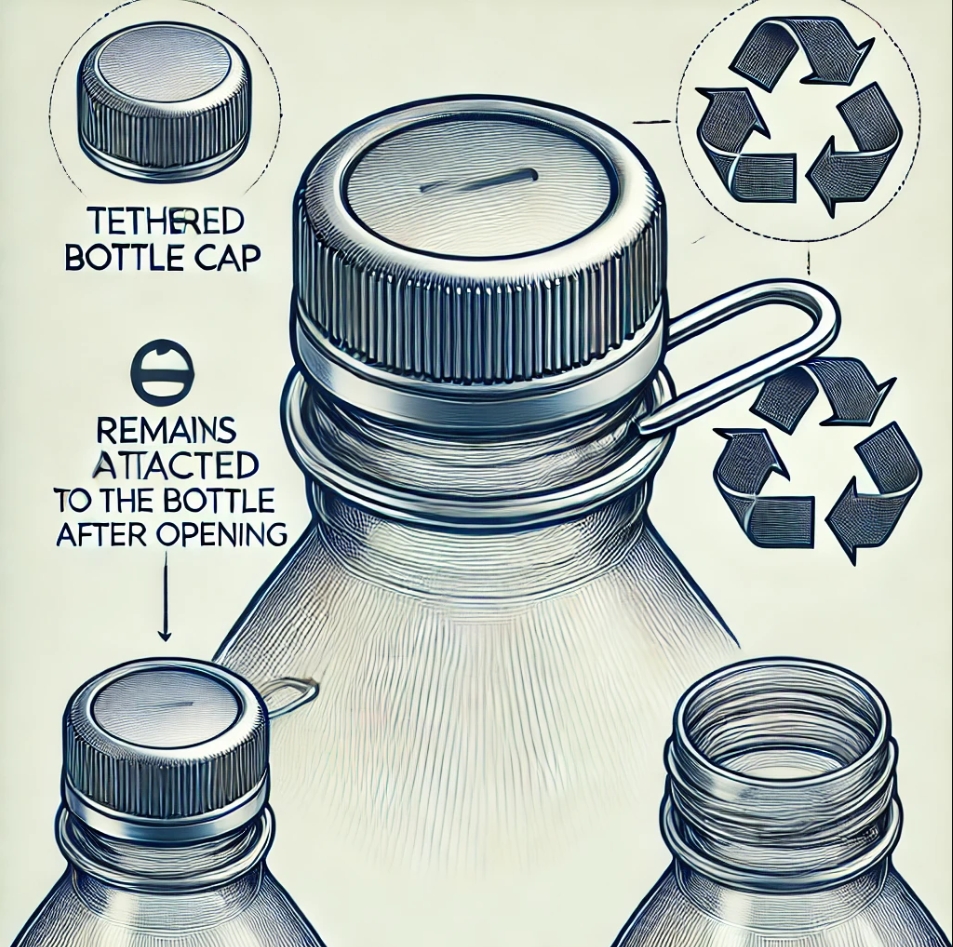
Exploration of Biodegradable and Bio-Based Plastics
Some manufacturers are researching bioplastics derived from renewable resources like corn starch and sugarcane. These materials reduce reliance on fossil fuels and, under certain conditions, may offer biodegradability, further minimizing plastic waste.
Ergonomic Considerations in Sustainable Cap Design
While sustainability remains a priority, ergonomics remains essential. Even as caps become lighter or made from alternative materials, manufacturers strive to ensure ease of opening and closing for consumers.
2. Sustainable Manufacturing Practices
Increased Use of Recycled Materials
The incorporation of Post-Consumer Recycled (PCR) plastics is now standard in cap production. By reprocessing waste plastic into new caps, manufacturers reduce dependency on virgin materials and divert waste from landfills.
Energy-Efficient Injection Molding
Advancements in injection molding technology are playing a crucial role in improving sustainability. Energy-efficient machinery, optimized cycle times, and heat recovery systems are now common in manufacturing facilities.
Key Improvements in Sustainable Injection Molding :
- Hybrid and Electric Injection Molding Machines – Reduce power consumption compared to traditional hydraulic systems.
- Closed-Loop Cooling Systems – Reuse cooling water, minimizing waste.
- Multi-Cavity Molds – Produce multiple caps per cycle, reducing energy use and improving efficiency.
- Precision Material Injection – Reduces excess plastic waste.
Machines like CLF’s TX Series and TWR/TPIIR Series ensure high efficiency and sustainability in plastic cap production.
Learn more : Energy-efficient Injection Molding Machines
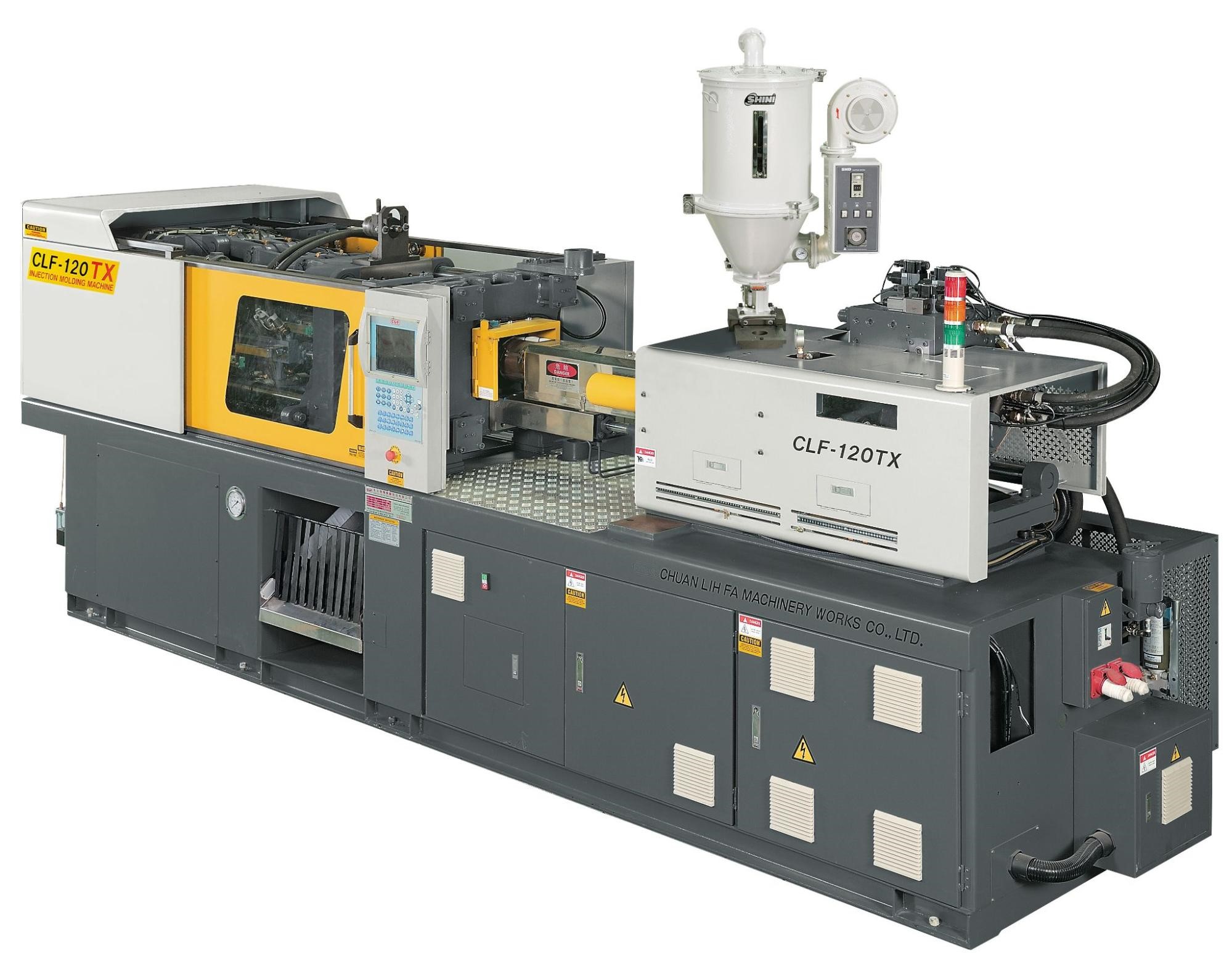
Adoption of Closed-Loop Manufacturing Systems
Some manufacturers are implementing closed-loop systems, where production waste is collected and reprocessed into new caps, minimizing waste and maximizing resource utilization.
Sustainable Supply Chain Practices
Beyond production, sustainability also involves responsible sourcing. Companies are selecting suppliers committed to renewable energy and ethical material sourcing, ensuring sustainability throughout the supply chain.
Life Cycle Assessments (LCA) for Environmental Impact
More manufacturers are utilizing Life Cycle Assessments (LCA) to evaluate the environmental impact of their products from raw materials to disposal. LCAs help guide material choices and process optimizations to lower carbon footprints.
Learn More : Plastic Cap Manufacturing and Sustainable Production Methods
3. External Factors Driving Sustainable Transformation
Stricter Regulations on Plastic Packaging
Many regions are introducing regulations that mandate recyclable materials, tethered caps, and reduced plastic use. These policies drive innovation in design and production.
Consumer Demand for Sustainable Packaging
Consumers are actively choosing brands that offer eco-friendly packaging, pushing companies to adopt greener cap designs and sustainable production methods.
4. The Role of CLF Injection Molding Machines in Sustainable Cap Production
CLF provides advanced injection molding solutions that support sustainable manufacturing. Our machines help brands reduce waste, improve energy efficiency, and optimize production costs.
Why Choose CLF for Sustainable Plastic Cap Manufacturing?
- Energy-Efficient Operations – Servo-electric and hybrid models reduce power consumption.
- Multi-Cavity Molds – Enable high-volume production while minimizing energy use.
- Optimized Material Utilization – Advanced resin control reduces waste and ensures consistent quality.
- Customization for Eco-Friendly Caps – Supports tethered, lightweight, and recyclable cap designs.
By choosing CLF’s injection molding machines, manufacturers can align with global sustainability trends and enhance their competitive edge in eco-friendly packaging.
Discover More : CLF’s sustainable injection molding solutions.
The Future of Sustainable Plastic Cap Manufacturing
The shift towards sustainability in plastic cap production is driven by regulatory changes, consumer awareness, and technological advancements.
By adopting eco-friendly materials, energy-efficient machines, and innovative cap designs, manufacturers can reduce their environmental impact while maintaining high-quality production.
With CLF’s advanced injection molding technology, companies can achieve sustainability goals and remain competitive in a rapidly evolving market.
Looking to invest in a high-performance injection molding machine for plastic caps? Consult with CLF today and discover how our cutting-edge solutions can help you optimize efficiency, reduce waste, and enhance your sustainability efforts.