Understanding Toggle Injection Molding Machines : Key Features, Benefits, and Smart Choices
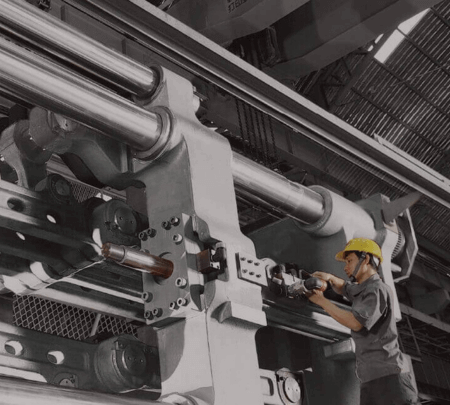
Injection molding is one of the most widely used manufacturing processes for producing plastic parts in large volumes. From automotive components to consumer electronics, industries rely on efficient and precise injection molding machines to meet production demands. Among the different types of clamping systems in injection molding machines, the toggle clamping mechanism stands out for its speed, energy efficiency, and high-volume capabilities. In this article, we will explore the features, benefits, and applications of toggle injection molding machines, with a comparative look at the traditional toggle system and the outward toggle system.

What is a Toggle Injection Molding Machine?
A toggle injection molding machine uses a mechanical linkage system to apply clamping force to the mold. This system typically consists of a series of levers connected in a toggle joint configuration, powered by a hydraulic or electric motor. During the clamping phase, the toggle mechanism extends, locking the mold tightly in place and withstanding the high pressure of molten plastic injection.
The toggle system is designed to quickly build up clamping force and maintain it throughout the injection and cooling phases. Once the molding cycle is complete, the mechanism retracts to open the mold and release the finished part. This clamping method is well-known for its ability to provide consistent clamping force while using less energy compared to fully hydraulic systems.
How Toggle Systems Work
The toggle mechanism operates through a series of interconnected levers that multiply the initial force input. During operation:
- The toggle mechanism extends to lock the mold in position
- Mechanical advantage maintains precise clamping force
- The system provides stable pressure throughout the injection cycle
- Once complete, the mechanism smoothly retracts for part removal
Key Features and Advantages of Toggle Injection Machines
Toggle injection molding machines offer several features that make them a popular choice for manufacturers across various industries:
-
High-Speed Clamping:
The mechanical advantage of the toggle system allows for rapid mold closing and opening, reducing cycle times and increasing overall productivity. -
Energy Efficiency:
Toggle machines require less hydraulic pressure and energy compared to fully hydraulic systems. The mechanical linkage multiplies the applied force, reducing the energy needed to achieve the same clamping force. -
Consistent Clamping Force:
Once fully extended, the toggle mechanism locks in place, maintaining consistent pressure throughout the injection cycle. This ensures part accuracy and reduces the risk of flash or deformation. -
Durability and Longevity:
Toggle systems experience less wear and tear compared to hydraulic systems due to their mechanical design, leading to longer machine life and lower maintenance costs. -
Reduced Operational Costs:
Lower energy consumption and maintenance requirements translate to reduced long-term operating costs.
Traditional vs. Outward Toggle Injection Molding Machines
-
Toggle Injection Machine (Traditional Toggle System)
The traditional toggle injection machine uses an inward-moving toggle mechanism, where the toggle arms move inward to lock the mold. This design has been widely adopted due to its high-speed clamping, energy efficiency, and ability to maintain consistent pressure throughout the injection cycle. However, the inward toggle mechanism requires more machine space and can make mold changes more complex, especially for larger molds. In CLF, our TX seris is the toggle injection machine. With a five-point internal toggle mechanism, it performs high-speed operation. Moreover, achieving energy saving and improved injection stability with customization.
Advantages:
- Fast clamping and opening speeds.
- High energy efficiency due to mechanical force multiplication.
- Ideal for high-volume, precision production.
Disadvantages:
- Larger footprint due to inward-moving parts.
- Less flexibility for quick mold changes.

Specifications of Traditional Toggle Injection Molding Machines
-
Outward Toggle Injection Machine
The outward toggle injection machine features a modified toggle system where the toggle arms move outward rather than inward. This design reduces the space required for machine operation and offers easier access to the mold area, simplifying mold installation and maintenance. Our TWII series, represents the outward toggle design injection machine, which has a five-point external toggle mechanism, showing low platen deformation and high precision. Besides, with customization to achieve ultra-long mold opening stroke that is suitable for longer, deeper or wider products, such as car bumpers.
Advantages:
- Space-saving design, ideal for factories with limited floor space.
- Easier and faster mold changes due to better mold area access.
- Better suited for large and complex molds, , such as car bumpers, making them ideal for a car bumper injection molding machine.
Disadvantages:
- Slightly more complex mechanism that may require more maintenance.

Specifications of Outward Toggle Type Injection Molding Machines
Comparison of Traditional Toggle vs. Outward Toggle Injection Molding Machines
The choice between a traditional toggle and an outward toggle injection machine depends on production needs. Traditional toggle machines are best for high-speed, high-volume production with standard mold sizes. Outward toggle machines are ideal for manufacturers needing space efficiency and frequent mold changes, especially for larger or more complex molds.
Common Applications of Toggle Injection Machines
Toggle injection molding machines are versatile and widely used across various industries due to their efficiency and adaptability. Common applications include:
-
Automotive Industry:
Toggle machines are ideal for producing precision automotive parts such as dashboards, bumpers, and interior trim components, where consistent quality and high-volume production are essential. -
Consumer Goods:
Products like household items, containers, and plastic furniture are commonly produced using toggle machines due to their cost-effective and high-speed production capabilities. -
Electronics Industry:
Small, intricate plastic components for electronic devices benefit from the precision and consistency offered by toggle machines. -
Packaging Industry:
Toggle machines are used to manufacture lightweight and durable packaging products, including bottle caps, containers, and storage bins. -
Medical Industry:
For high-precision, sterile medical components, toggle machines provide the accuracy and repeatability required to meet industry standards. -
Plastic Pallets:
Manufacturers can utilize a plastic pallet injection molding machine to produce durable and high-quality plastic pallets for various logistics and storage needs.





Selecting the Ideal Toggle Injection Molding Machine
Toggle injection molding machines remain a cornerstone of modern plastic manufacturing, offering high-speed production, energy efficiency, and durability. The traditional toggle system is well-suited for high-volume production runs requiring precision and speed, while the outward toggle design provides space-saving advantages and easier mold changes for more complex manufacturing needs.
Additionally, understanding how to calculate injection molding tonnage is essential for selecting the right machine, ensuring it can handle the required clamping force for your specific application.
As industries continue to demand greater efficiency and sustainability, investing in the right injection molding technology will be critical for maintaining competitiveness. Whether for plastic injection molding machine solutions or specialized equipment like a two platen injection molding machine, toggle injection molding machines offer the performance and versatility to meet evolving market demands.
Check our TX series or TWII series to find out your best plastic solution, , whether you're in need of a car bumper injection molding machine or exploring options for plastic pallet injection molding machines. With the right machine, your production can achieve unparalleled efficiency and precision.