How to Calculate Injection Molding Tonnage : A Step-by-Step Guide
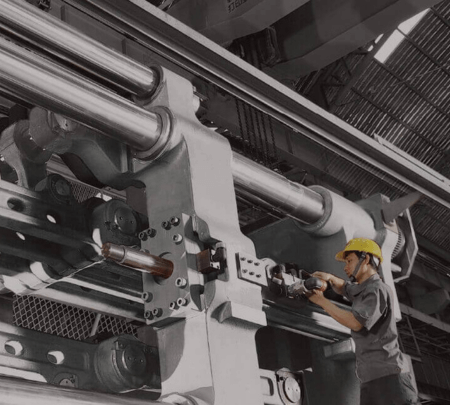
Injection molding is a versatile and precise manufacturing process essential for various industries, from automotive and electronic devices to medical and consumer goods. To ensure successful molding outcomes, understanding how to calculate the necessary clamping tonnage for your injection molding machine is crucial. Accurate tonnage calculations help prevent mold damage, ensure consistent part quality, and optimize production efficiency.
1. Understanding Tonnage in Injection Molding
Injection molding is a complex manufacturing process that involves injecting molten material into a mold cavity, where it solidifies to form a desired part. Central to this process is the clamping unit of the injection molding machine, which applies force to hold the mold closed with sufficient pressure during injection. Without adequate clamping force, the mold may not be able to withstand the pressure exerted by the injected material, leading to issues such as flash, short shots, or even mold damage.
Now, let's delve deeper into the reasons why clamping force is essential in injection molding :
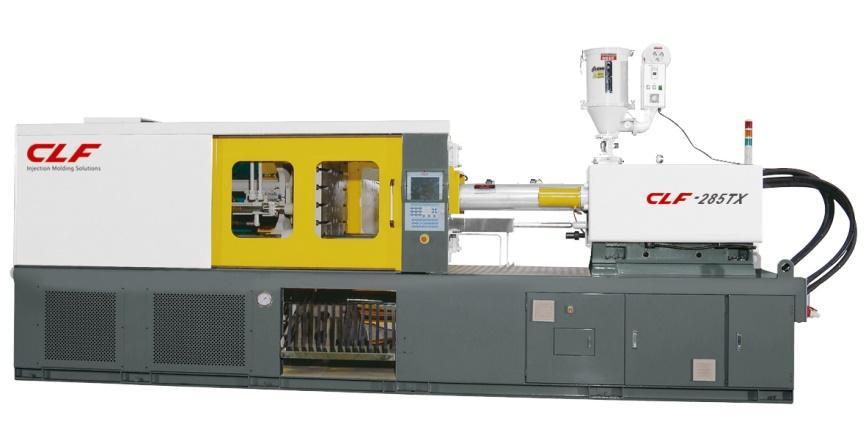
- Preventing Mold Damage :
- Ensuring Part Quality :
- Optimizing Production Efficiency :
Insufficient clamping force can result in mold flashing (material squeezing out) or short shots (incomplete filling). Conversely, excessive clamping force can cause mold damage and unnecessary wear and tear.
Proper clamping force ensures consistent part dimensions, reduces the risk of defects like warpage or voids, and maintains product integrity.
Accurate tonnage calculations help select the right machine for the job, minimize cycle times, and maximize production output.
2. Factors Affecting Tonnage Calculations
Injection molding is a nuanced process influenced by multiple factors, each contributing to the determination of the required clamping tonnage. These factors are pivotal in ensuring the successful execution of the molding process, as they directly impact mold stability, part quality, and overall production efficiency. Let's delve deeper into these factors :
- Material Type :
- Part Geometry :
- Mold Design :
Different plastics exhibit varying viscosities and melt flow characteristics. Higher viscosity materials such as polycarbonate (PC) or polysulfone (PSU) typically require greater clamping force compared to lower viscosity materials like polyethylene (PE) or polypropylene (PP).
The shape and structure of the parts being molded also play a significant role in determining the required tonnage. Parts with large projected areas, intricate details, or thick-walled sections often demand increased tonnage to maintain mold stability.
The complexity of the mold design can impact clamping force requirements. Multi-cavity molds, molds with complex side actions, or those incorporating hot runner systems may necessitate higher clamping forces to ensure proper mold closure and part formation.
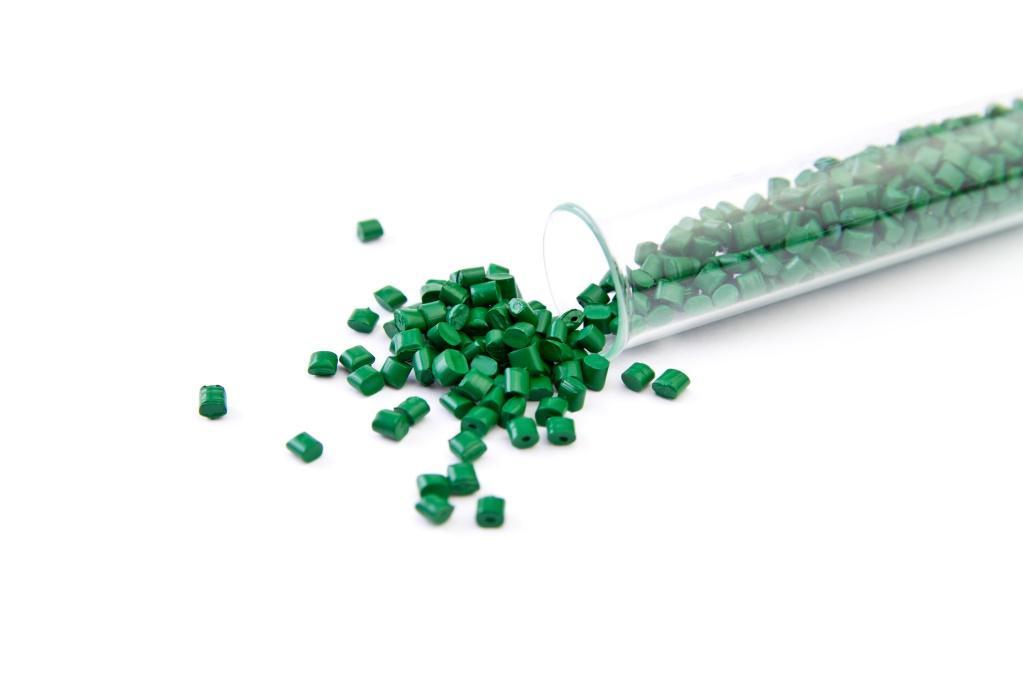
3. Tonnage Calculation Formulas and Methods
Calculating injection molding tonnage involves various methods, each offering its own set of advantages and complexities. These methods range from quick empirical formulas to sophisticated computer-aided engineering (CAE) software simulations, providing manufacturers with flexible options to determine the clamping force required for their specific molding processes.
Method 1 : Empirical Formula #1
This simple formula provides a quick estimate of clamping force :
Clamping Force (Tons) = Clamping Force Constant (Kp) * Projected Area (sq in) * Safety Factor (usually 1.2)
Example :
Calculate the clamping force for a product with a projected area of 100 sq in from ABS (Kp = 2.5 ton/in2) :
Clamping Force (Tons) = 2.5 * 100 * 1.2 = 300 tons
Therefore, you need at least around 300 tons of plastic injection molding machine.
Clamping Force Calculator :
Best Practices for Injection Molding Machine Selection and Tonnage Adjustment
Apart from calculating tonnage, selecting the appropriate injection molding machine is also crucial. Considering factors such as part size, material characteristics, and mold design, choosing an injection molding machine with the appropriate tonnage can maximize production efficiency and ensure part quality. Additionally, tonnage adjustment may be necessary during the production process to address different production requirements, requiring operators to have the necessary skills and experience.
- Customized Plastic Injection Machines : Discover how we can tailor an injection molding machine to meet your specific requirements, including large-scale applications.
- 2024 Injection Molding Machine Trends : Stay ahead of the curve with our insights into the latest industry trends and technologies.
- Essential Features of PET Preform Injection Molding Machines : Learn about the key features to consider when selecting a PET preform injection molding machine.
- All You Need to Know About Plastic Pallet Injection Molding Machines : Get a comprehensive overview of plastic pallet injection molding machines and their applications.
Contact us today for a free consultation and let our experts help you achieve your injection molding goals!