3 Key Factors Impacting Production Efficiency in Plastic Injection Molding Machines
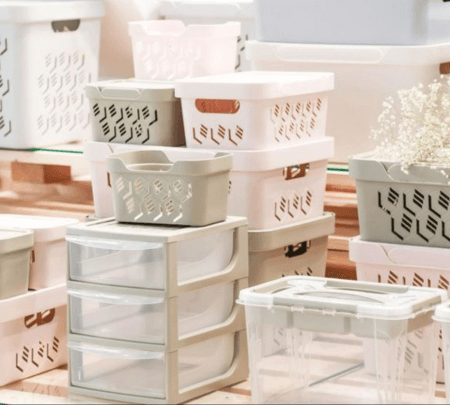
Production efficiency in plastic injection molding is essential for maintaining competitiveness in the manufacturing industry. Efficiency not only affects output quantity but also influences the quality and cost-effectiveness of the final products. By focusing on specific factors, manufacturers can optimize their processes, reduce waste, and achieve higher productivity. We are going to explore the key elements that impact efficiency in plastic injection molding machines, including material and machine parameters, mold design, automation, and Digital Solutions Improve Plastic Injection Molding Precision, Efficiency, and Quality.
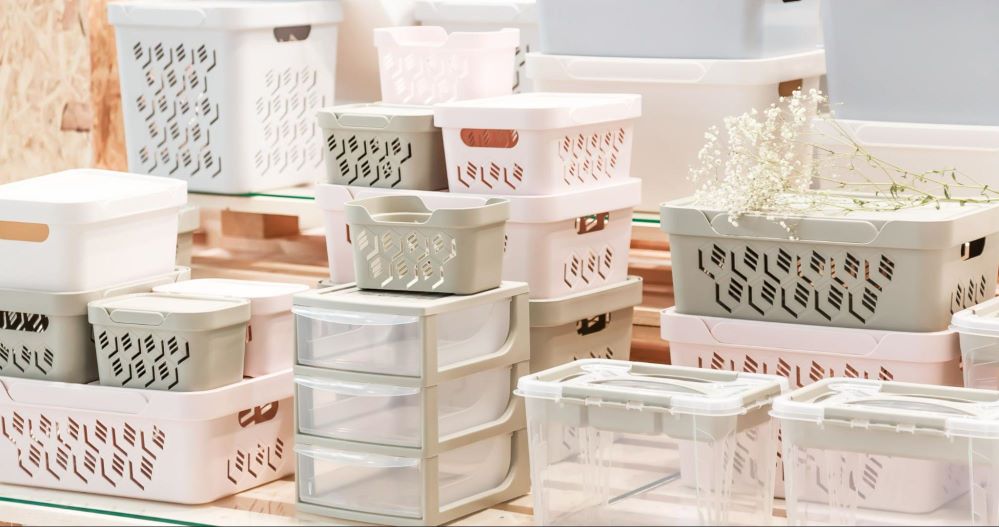
1. Material and Machine Parameters
One of the most critical factors in injection molding efficiency is the selection of the right materials. Material properties such as melt flow rate, thermal conductivity, and shrinkage impact the molding process. Using high-quality, compatible materials reduces the likelihood of defects and enhances production speed. In addition to material selection, machine parameters such as clamping force, injection pressure, and cooling time play a vital role in shaping production efficiency.
For instance, the clamping force must be strong enough to hold the mold tightly during injection to avoid flash—a defect that occurs when excess plastic leaks out of the mold. Likewise, the injection pressure must be optimized to ensure the molten plastic fills the mold cavity evenly. Cooling time, on the other hand, should be minimized without compromising part quality, as it significantly affects cycle time. By fine-tuning these machine parameters, manufacturers can achieve more consistent and faster production cycles.
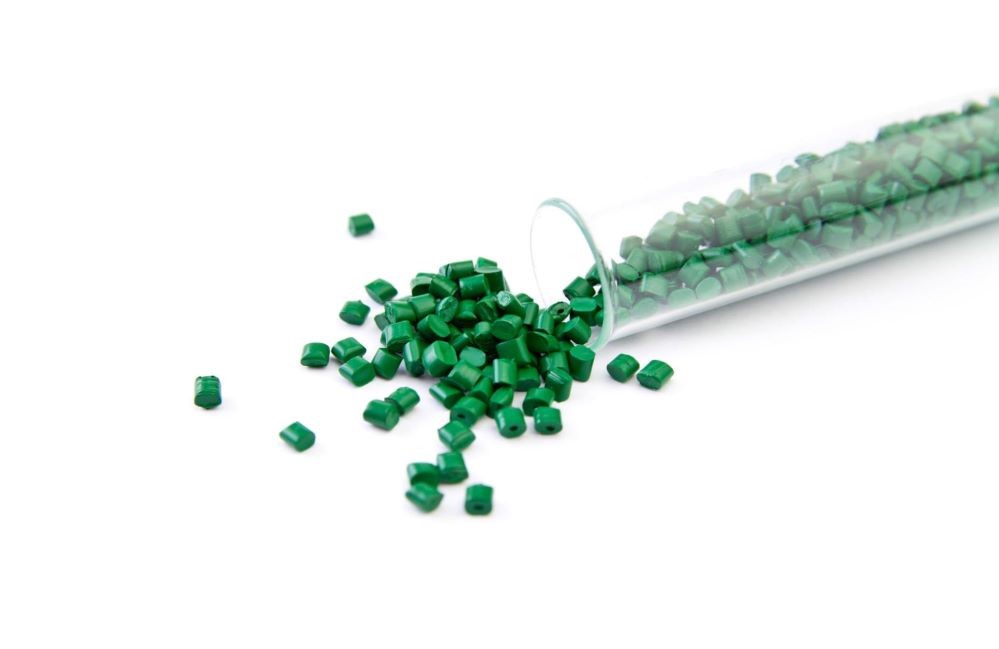
2. Mold Design and Automation
Mold design is another major contributor to production efficiency. A well-designed mold facilitates smooth plastic flow, reducing the chance of defects like warping or short shots. Key elements of mold design include gate layout, runner system, and temperature control. For example, a balanced runner system ensures equal distribution of molten plastic to each cavity, especially in multi-cavity molds. Temperature control features, such as cooling channels, help maintain a uniform temperature within the mold, which can speed up the cooling phase and improve cycle time.
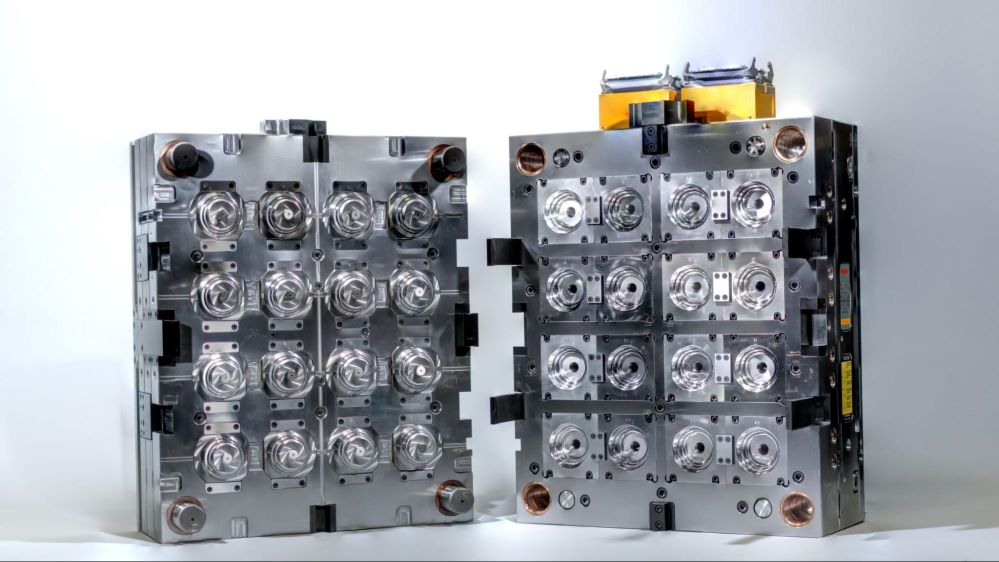
Furthermore, modern mold designs can incorporate techniques such as In-Mold Labeling (IML), which integrates labeling directly into the molding process. This technique not only enhances the aesthetic appeal of the final product but also reduces additional labeling costs and improves production efficiency.
Automation also plays a significant role in the injection molding process. Automated systems can perform repetitive tasks, such as material feeding, part removal, and packaging, with high precision and speed. This reduces the need for human intervention, which in turn lowers the risk of errors and increases productivity. Moreover, automation enables manufacturers to implement smart robotics for complex tasks, enhancing consistency and quality. Automated equipment not only saves time but also frees human operators to focus on more value-added tasks.
3. Digital Solutions and Maintenance
In today’s manufacturing landscape, digital solutions are essential for maintaining efficiency in plastic injection molding. Technologies such as the Internet of Things (IoT) enable real-time monitoring of machinery, providing insights into machine performance and identifying potential issues before they become critical. For example, IoT sensors can track parameters like temperature, pressure, and vibration levels, which helps operators optimize the molding process and quickly respond to abnormalities. Digital twins, virtual models of physical assets, allow manufacturers to simulate the injection molding process, experiment with different variables, and predict potential problems.
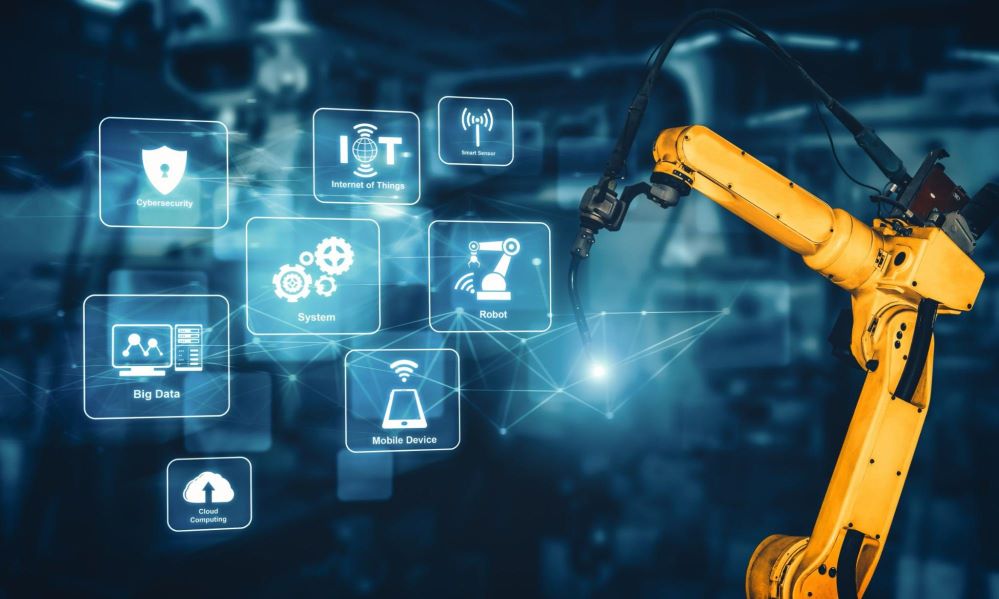
Preventive maintenance is another critical factor in ensuring production efficiency. With the help of digital solutions, manufacturers can schedule maintenance activities based on real-time data rather than relying on fixed schedules. This approach, known as predictive maintenance, minimizes unexpected downtime and extends the lifespan of machinery. By combining digital monitoring tools with a proactive maintenance strategy, manufacturers can ensure their injection molding machines, including Large Plastic Injection Machines, operate at peak efficiency and avoid costly production delays.
Enhancing Production Efficiency:Key Takeaways
Maximizing production efficiency in plastic injection molding requires a holistic approach that considers material selection, machine optimization, mold design, automation, and digital technologies. Fine-tuning machine parameters and investing in well-designed molds enhance production speed and consistency. Leveraging automation reduces manual errors and improves productivity, while digital solutions like IoT and digital twins offer real-time insights and predictive maintenance capabilities. Furthermore, implementing advanced machinery such as the Two Platen Injection Molding Machine can enhance operational flexibility and efficiency, further boosting overall productivity. By focusing on these factors, manufacturers can streamline operations, improve product quality, and maintain a competitive edge in the global market.
In addition, CLF's Support for Injection Molding Solutions in ASEAN/Southeast Asia plays a vital role in helping manufacturers in this region enhance their production capabilities. By focusing on these factors, manufacturers can streamline operations, improve product quality, and maintain a competitive edge in the global market.
To further empower your automotive manufacturing processes, download our free eBook, “Revolutionize Your Automotive Manufacturing with CLF's Injection Molding Solutions” Discover how CLF's expertise can provide innovative solutions for performance, sustainability, and aesthetics in your production of high-quality auto parts. Fill out the form below to access your copy and start transforming your manufacturing journey today!
eBook : Revolutionize Your Automotive Manufacturing with CLF's Injection Molding Solutions Download Now !
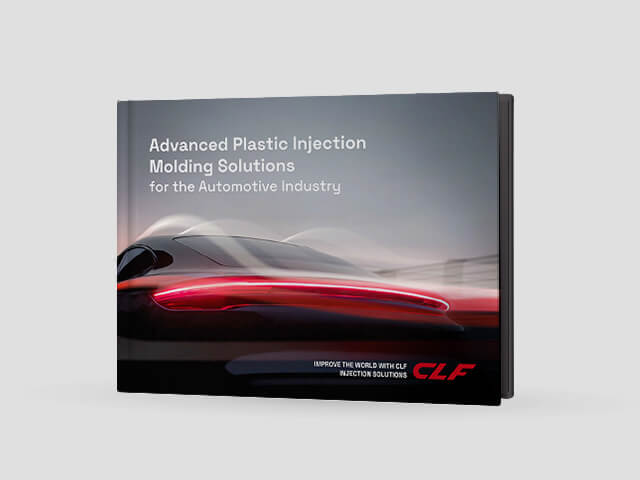
With CLF, a professional leader in manufacturing plastic injection molding machines, we can help you customize a high-efficiency injection solution. Contact CLF today to discover your best business opportunity!