Injection Molding Machine Troubleshooting : Solutions for Common Problems
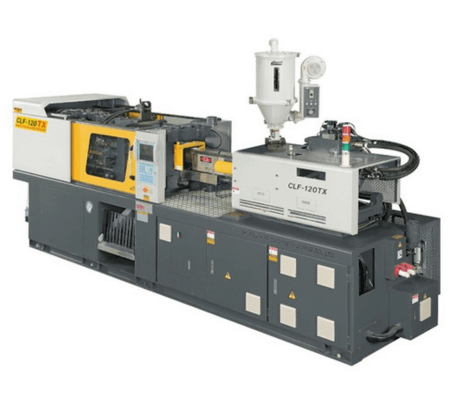
Plastic injection molding machines are vital to modern manufacturing processes, producing components with precision and efficiency. However, like any complex machinery, they are susceptible to various operational issues. Identifying these problems early and resolving them effectively is critical to maintaining productivity and avoiding costly downtime. This article explores seven common problems encountered in plastic injection molding machines and offers practical solutions to address them.
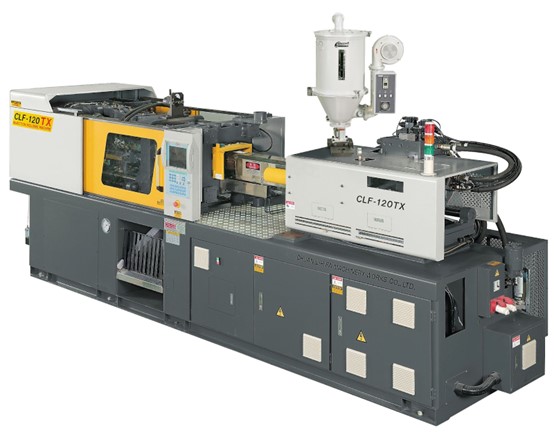
Nozzle or Gate Blockage
Issue:
Material clogging the nozzle or gate disrupts the flow, leading to improper injection and potential defects in the molded product.
Solution:
Regularly clean the nozzle and gate to remove any debris or material buildup. It is also essential to check their alignment and maintain appropriate heating temperatures to ensure smooth material flow. Preventive maintenance and monitoring can further reduce the likelihood of clogs.
Excessive Vibration
Issue:
Excessive vibrations in the machine can affect the precision and consistency of the molded parts, as well as cause wear on components.
Solution:
Inspect and tighten any loose components to minimize vibration. Replace worn-out parts and ensure that all moving components, such as the platen and clamping units, are properly aligned. Maintaining optimal operating conditions will help reduce unnecessary movement.
Hydraulic Oil Leaks
Issue:
Hydraulic oil leaks can compromise machine efficiency, contaminate the working environment, and pose safety hazards.
Solution:
Inspect the hydraulic system regularly for signs of damage or wear, such as cracks in seals, hoses, or fittings. Replace faulty components immediately and ensure the hydraulic system operates within recommended pressure levels. Routine maintenance is critical to preventing leaks and extending the system's lifespan.
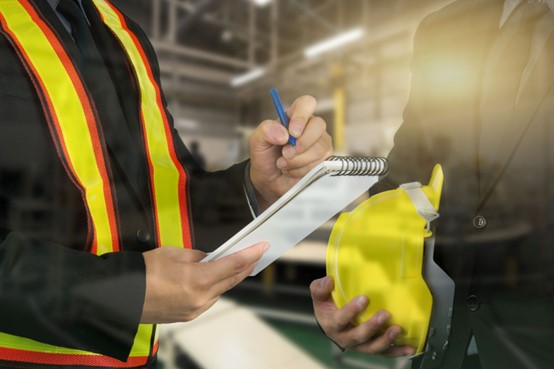
Ejector System Malfunction
Issue:
If the ejector system fails, molded parts may not release properly, leading to deformation, defects, or machine downtime.
Solution:
Lubricate ejector pins regularly to ensure smooth operation and check their alignment to prevent sticking. Routine inspection and maintenance of the ejector mechanism will help avoid malfunctions, ensuring parts are released properly without damage. Additionally, it’s crucial to monitor three related issues : if pressure is insufficient, consider increasing the hydraulic cylinder size; for inadequate mold opening, upgrading to a machine with higher clamping force may be necessary; and if the ejector plate is uneven, inspect for potential damage to the mold base support pillars and replace them as needed.
Screw Slippage
Issue:
When the screw does not transport material efficiently, it can result in inconsistent shot sizes, affecting the quality of molded parts.
Solution:
Inspect the screw and barrel for signs of wear or contamination. Clean them thoroughly to maintain optimal performance. Additionally, verify that back pressure and screw speed settings are correctly calibrated to enhance material transport and consistency.
Electric Motor Overheating
Overheating electric motors reduce efficiency and increase downtime due to potential damage or the need for repairs.
Solution:
Ensure that motors are adequately ventilated by cleaning fans and filters regularly. Verify that load levels are within the manufacturer’s specifications and avoid overloading the system. Monitoring motor performance can prevent overheating and ensure consistent operation.
Barrel Wear and Tear
Issue:
Over time, barrels experience wear and tear, leading to poor material flow and inconsistent injection performance.
Solution:
Regularly inspect the barrel for signs of damage or erosion. Replace worn-out barrels or screws as needed to maintain efficiency. Proper material handling and cleaning can also prolong the life of these components.
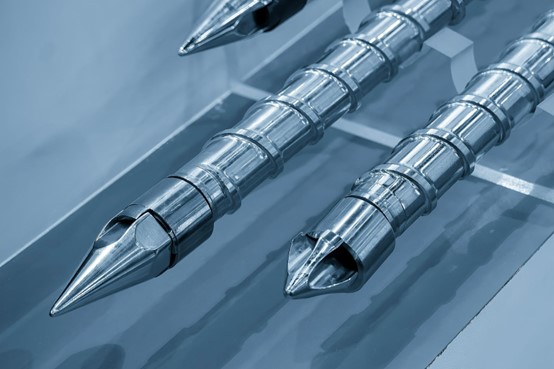
Addressing common plastic injection molding machine problems promptly and effectively is essential to maintaining productivity and delivering high-quality products. Regular maintenance, including cleaning, inspection, and timely replacement of worn-out parts, plays a crucial role in minimizing downtime and ensuring smooth operations. By adopting a proactive approach to problem-solving and adhering to best practices, manufacturers can enhance the performance and longevity of their injection molding machines, ensuring reliable production and maximizing their investment.
The proper functioning of complex machinery like two-platen injection molding machines is critical for ensuring high productivity in demanding industries, including automotive injection molding. Addressing common plastic injection molding machine problems promptly and effectively is essential to maintaining productivity and delivering high-quality products. Regular maintenance, including cleaning, inspection, and timely replacement of worn-out parts, plays a crucial role in minimizing downtime and ensuring smooth operations.
For example, pet injection molding machines are used to create various precision components, including those used in pet preform manufacturer processes. Similarly, bumper molding applications rely on accurate injection molding tonnage calculations to achieve optimal results. By adopting a proactive approach to problem-solving and adhering to best practices, manufacturers can enhance the performance and longevity of their injection molding machines, ensuring reliable production and maximizing their investment.
Looking to dive deeper into advanced techniques and solutions? Explore our eBook on "Automotive Injection Molding" for comprehensive insights and strategies to optimize your processes. Click here to discover more and transform your operations today!