Optimizing Injection Molded Automotive Parts : 3 Essential Strategies
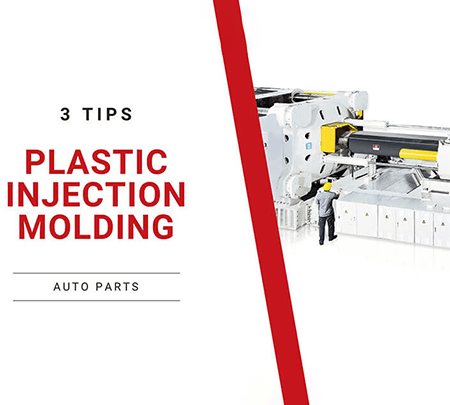
Plastics are indispensable in the modern automotive industry, replacing metal components to make vehicles lighter, more fuel-efficient, and cost-effective. From bumpers and dashboards to headlamps and door panels, injection molded automotive parts are vital for achieving these goals. To produce high-quality automotive components, manufacturers must carefully consider design, materials, and machine customization.
In this guide, we’ll explore three essential tips to optimize your production of injection molded automotive parts while meeting the demands of quality and efficiency.
-
Understand the Characteristics of Injection Molded Automotive Parts
Recognizing the unique features and requirements of different automotive components is the first step in selecting the right injection molding solution. Here are the four main categories of injection molded automotive parts
-
Interior Parts
Interior components such as dashboards, roof linings, door handles, center consoles, car mats, and dashboard compartments are injection molded for their precision and durability. For complex designs like dashboards or door panels, secondary processes such as in-mold labeling or multi-shot molding may be necessary to achieve a premium finish.
-
Exterior Parts
Exterior parts, including bumpers, grilles, fenders, side mirrors, and step bumpers, require high aesthetic quality and lightweight designs. Injection molding machines with co-injection capabilities are ideal for producing multi-colored or textured finishes for exterior automotive components. The trend toward lightweight designs has also caused adjustments in machine design.
-
Under-the-Hood Components
Engine accessories, including oil pans, cylinder head covers, sensors, and battery cases, are increasingly made from durable plastics. Fiber-reinforced materials such as nylon or polycarbonate require machines with specially designed screws and molds to handle these demanding applications.
-
Lighting Systems
Lighting components like headlamps and signal lights demand exceptional precision and clarity. Due to their complicated mold design and strict inspection standards, advanced temperature control and precision mold design are essential for achieving defect-free, high-quality finishes.
-
-
Choose the Right Materials for Injection Molded Automotive Parts
Selecting the appropriate materials is crucial for producing durable, high-performing automotive parts. Here are some commonly used materials in injection molded automotive parts production:
-
Polypropylene (PP)
Lightweight and chemical-resistant, PP is widely used for bumpers, dashboards, and radiator components. Adding fiberglass improves its strength.
-
Polycarbonate (PC)
Durable and heat-resistant, PC is ideal for clear and smooth lighting components.
-
Acrylonitrile Butadiene Styrene (ABS)
Known for its heat resistance and glossy finish, ABS is commonly used in dashboards and wheel covers.
-
Nylon (Polyamide)
Strong and wear-resistant, often reinforced with fiberglass for enhanced properties. Used for bushes and bearings.
-
Polyurethane (PU)
Flexible and abrasion-resistant, PU is used in foam seating and seals. Common defects like yellowing or surface irregularities can be minimized by controlling heating temperatures.
-
Polyvinyl Chloride (PVC)
Versatile for both hard and soft parts, PVC is flame retardant but requires environmentally friendly alternatives like TPU or ABS for certain applications.
-
Reinforced Composites
Glass or carbon fiber-reinforced plastics are strong and lightweight, ideal for structural components like bumpers and body panels.
-
-
Customize Injection Molding Machines for Automotive Excellence
Customization is key to meeting the unique production demands of injection molded automotive parts. Based on CLF’s experience, here are some recommended features and advanced capabilities of modern injection molding machines:
-
Lightweight Production:
Machines designed to handle larger molds with smaller clamping forces or process fiber-reinforced materials, ensuring strength without sacrificing weight. -
Enhanced Productivity:
Machines capable of multi-step operations, such as co-injection or over-molding, streamline production processes and reduce cycle times. -
High Precision:
Advanced temperature and mold control systems ensure consistent quality for high-precision components like lighting systems. These systems help reduce defects and ensure a smooth surface finish. -
Space-Saving Design:
Two-platen injection molding machines save space while maintaining efficiency for large-scale production. -
Energy Efficiency:
Equipped with servo-driven hydraulic systems or all-electric technology, modern machines reduce energy consumption, lowering operational costs. -
User-Friendly Controls:
Intuitive interfaces and real-time monitoring systems simplify operations, allowing for precise adjustments during production. -
Durability and Reliability:
Built with high-grade materials, these machines offer long operational life and minimal downtime, even under demanding conditions. -
Customizable Features:
Options like multi-color injection, gas-assisted molding, or mold temperature control systems ensure flexibility for a wide range of applications.
-
-
Case Studies: Real-World Success with Injection Molded Automotive Parts
Injection molding has transformed the production of automotive parts. From dashboards requiring intricate designs to lightweight bumpers made with reinforced composites, the potential for innovation is vast.
Case Highlight : TWII Series for Car Bumper Molding
The TWII Series outward toggle type plastic injection molding machine is a standout solution for producing car bumpers with precision and efficiency. With clamping forces ranging from 90 to 5000 tons, it offers:
-
Center-Focused Clamping Force:
Ensures even distribution across the mold, minimizing platen deformation and delivering higher product precision.
-
High Precision Injection Mechanism:
Supported by linear slide rails for smooth movement, low friction, and exceptional accuracy.
-
Customizable Mold Opening Stroke:
Ideal for producing deeper products, the mold opening stroke can be extended to meet specific production requirements.
-
Energy-Saving Features
Options include energy-saving servo drives, electric material storage for enhanced plasticization, and efficient material tube heating solutions.
-
Rigidity and Stability
The five-point external toggle mechanism ensures high platen rigidity and precision, making it suitable for high-surface-precision and deep-depth products.
-
With these advanced features, injection molding machines are perfectly equipped to meet the stringent requirements of automotive manufacturing.
Read further : 5 Essential Features for Plastic Injection Molding in Automotive Industry
These features make the TWII Series an ideal choice for automotive manufacturers seeking reliable and customizable solutions for car bumper production.
Bonus Tip : Revolutionize Your Automotive Manufacturing
To further enhance your expertise in producing injection molded automotive parts, download our free eBook : Revolutionize Your Automotive Manufacturing with CLF's Injection Molding Solutions. This resource provides invaluable insights into design optimization, material selection, and machine customization to help you stay ahead in automotive manufacturing.
Bringing It All Together : Optimizing Automotive Injection Molding
Producing high-quality injection molded automotive parts requires a blend of precision, material expertise, and machine customization. By understanding the unique characteristics of automotive components, choosing the right materials, and tailoring your injection molding machines, you can optimize your automotive injection molding production processes and meet the evolving demands of the automotive industry.
At CLF, we offer advanced injection molding solutions tailored to your needs. Contact us today to learn more, or you can check out the product page for more exclusive injection molding machines for car bumpers. and view our other series of injection molding machines.