A Comprehensive Guide to Injection Molding Machine Maintenance
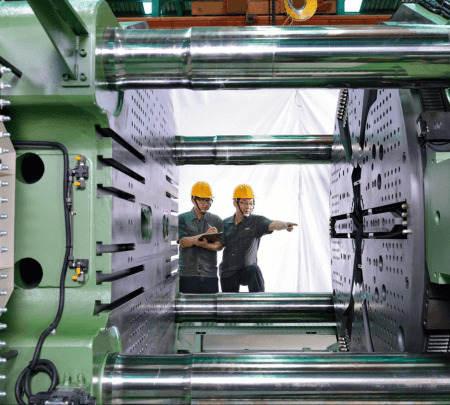
Plastic injection molding machines, including specialized types like the two-platen injection molding machine, are significant investments in any manufacturing facility. Extending their lifespan through proper maintenance not only helps maximize return on investment but also ensures consistent production quality, minimizes downtime, and enhances operational efficiency. Routine injection molding machine maintenance is essential for preventing unexpected breakdowns, reducing costly repairs, and maintaining high-quality output across industries. This guide provides essential maintenance tips to help you safeguard your injection molding machine’s performance, enabling you to get the most from your equipment year after year.
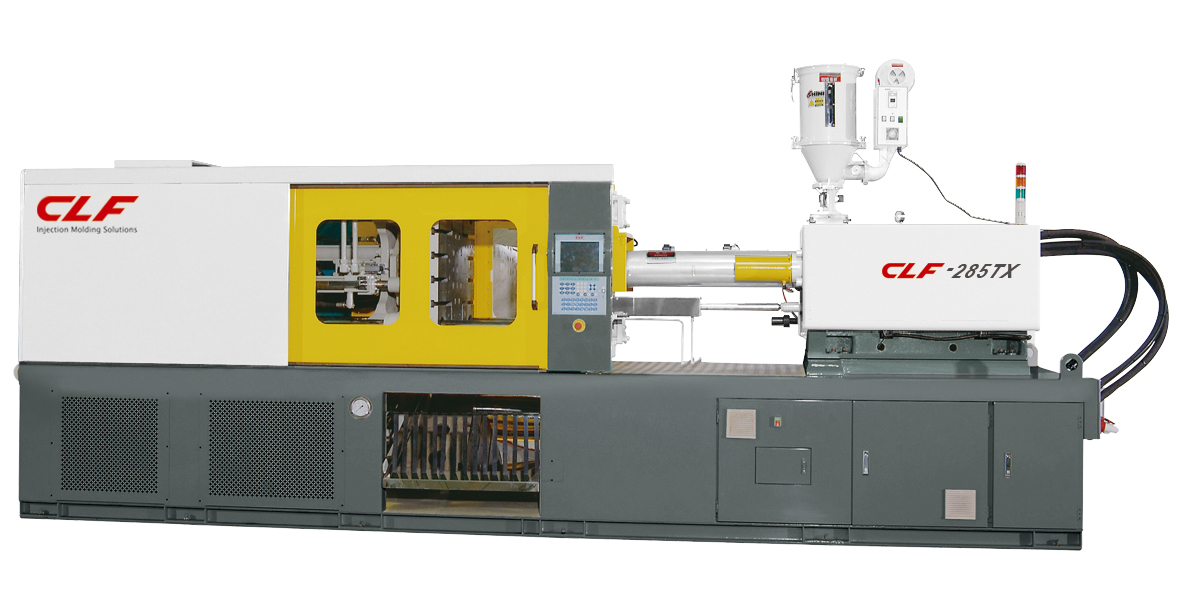
Regular Cleaning and Inspection
Routine injection molding machine maintenance begins with cleaning and thorough inspection.Over time, buildup from materials and residues can accumulate on the mold and barrel, which impacts product quality and machine performance. Implementing a cleaning schedule helps maintain the injection molding machine's efficiency and prevents potential damage.
-
Inspect Mold and Barrel:
Regularly inspecting the mold and barrel for residue buildup prevents imperfections in molded parts, which can arise from contamination. This essential maintenance step keeps your machine running at peak performance. -
Monitor for Wear and Tear:
Identifying signs of wear, such as scratches, dents, or loose screws, allows you to take preventive actions and avoid extensive repairs.
By incorporating regular inspections into your maintenance routine, you can identify early warning signs and maintain high productivity.
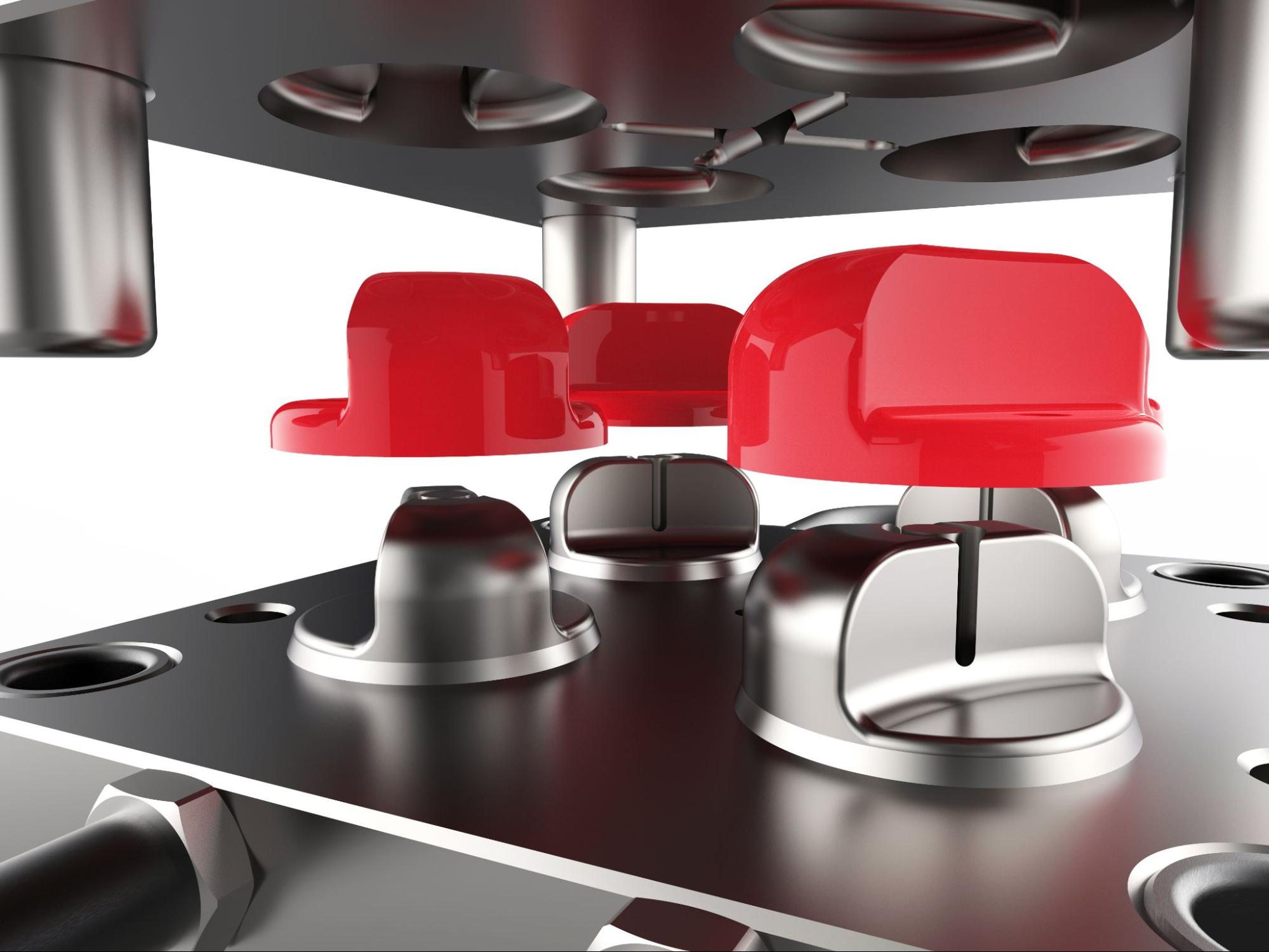
Lubrication of Moving Parts
Lubrication is a core part of injection molding machine maintenance that reduces friction—a primary cause of wear in injection molding machines. Consistently lubricating moving parts ensures smoother operations and minimizes strain on the machine, ultimately extending its life.
-
Focus on Clamping Mechanisms and Injection Units:
The clamping mechanisms and injection units are the machine’s primary moving parts and therefore require the most attention when it comes to lubrication. Proper lubrication ensures smoother movements, reduces wear, and prevents overheating. -
Choose the Right Lubricant:
It’s essential to use the right type of lubricant as specified by the machine manufacturer. Some machines require specific lubricants that provide optimal performance, so always refer to the manufacturer’s recommendations. -
Set a Lubrication Schedule:
Depending on the machine’s usage, establish a regular schedule for lubrication. Heavily used machines may require more frequent lubrication than those that operate less often. Consistent application helps maintain machine precision and reliability.
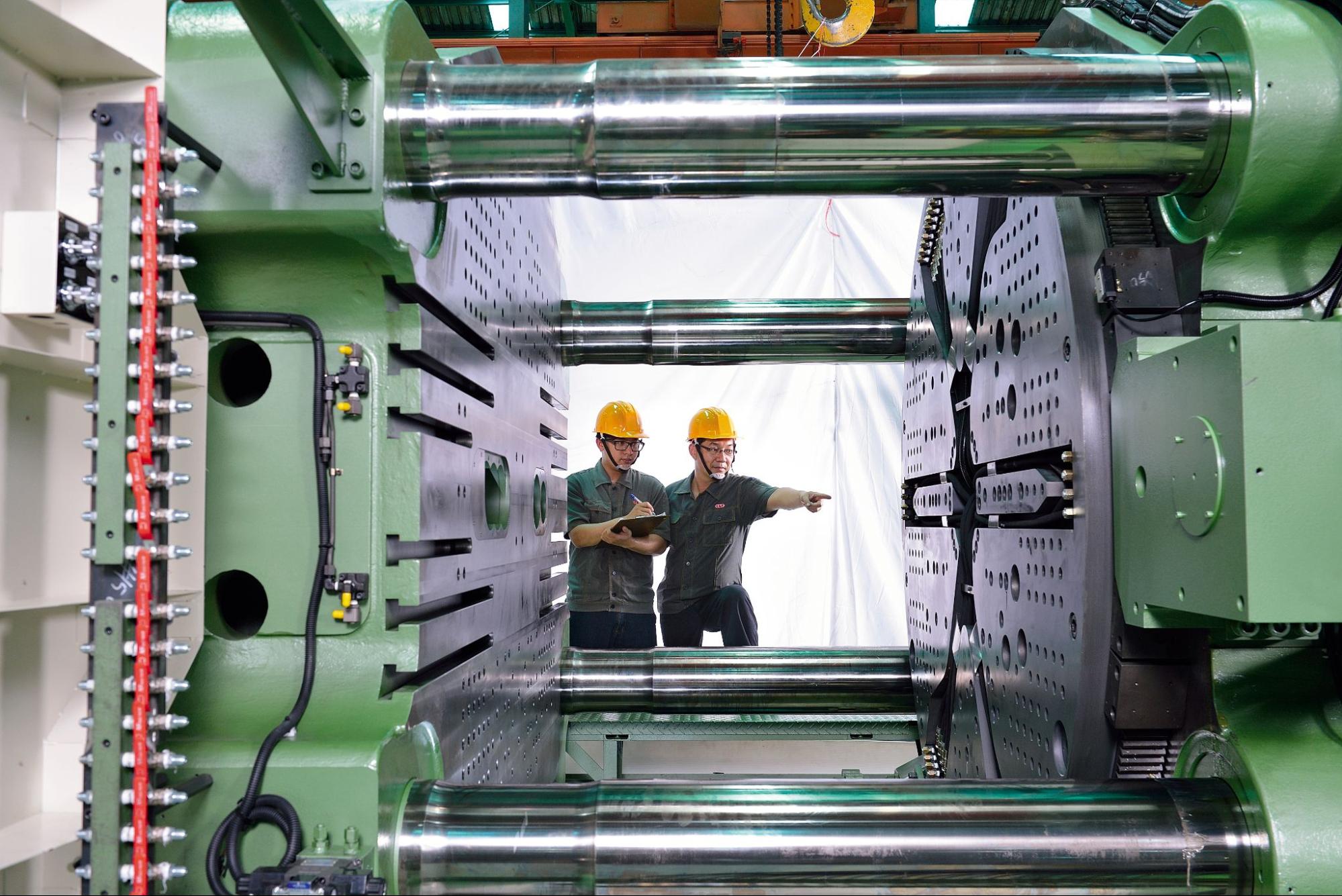
Monitoring Key Machine Parameters
Advanced injection molding maintenance practices include digital monitoring systems that track key machine parameters in real-time. Monitoring these parameters can help identify potential problems before they cause malfunctions, preserving both productivity and machine lifespan.
-
Track Temperature and Pressure:
Temperature and pressure are crucial to the injection molding process. Sudden changes in these parameters could indicate potential issues with the machine, such as cooling system failures or problems with the heating elements. Real-time monitoring provides insights and helps you catch issues before they escalate. -
Monitor Cycle Times:
Cycle time directly affects production efficiency. A change in cycle time may signal an underlying issue with the machine, such as component misalignment or worn parts. Regularly tracking cycle times can help detect issues that impact productivity and machine health. -
Leverage Digital Solutions:
Many modern injection molding machines come with digital monitoring solutions that allow operators to view and manage performance data remotely. Leveraging these digital tools enhances accuracy, enables proactive maintenance, and supports a data-driven approach to machine management.
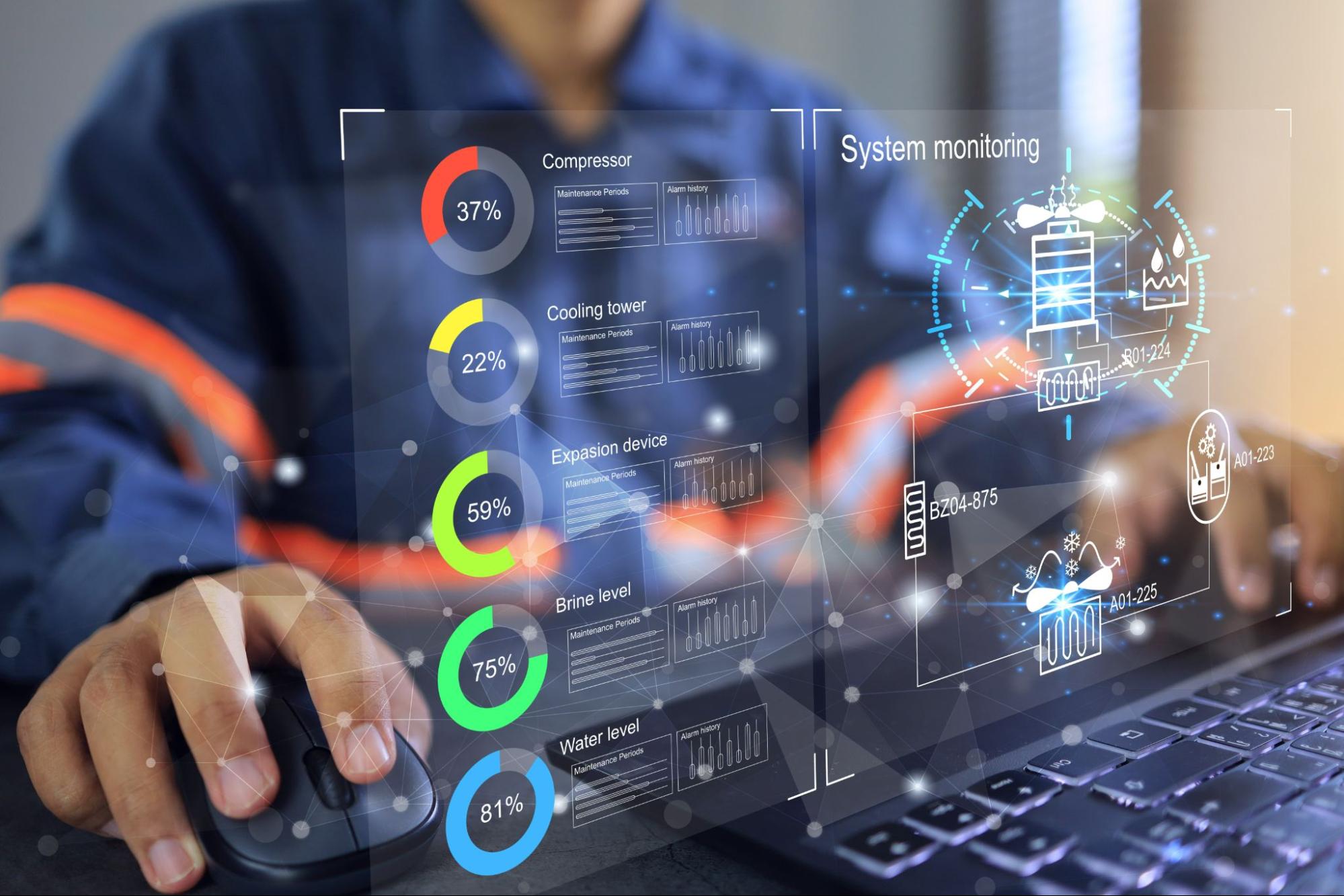
Accurate tonnage calculations are essential to avoid overloading or underutilizing the machine. Read more:How to Calculate Injection Molding Tonnage: A Step-by-Step Guide to understand how to determine the ideal tonnage for your molding projects.
Common Injection Molding Maintenance Mistakes to Avoid
Maintaining an injection molding machine can be challenging, and even small mistakes can result in costly repairs or reduced machine life. Avoiding these common maintenance errors can save time and money:
-
Neglecting Regular Inspections:
Skipping inspections allows small issues to escalate, often resulting in expensive repairs. -
Using the Wrong Lubricants:
Incorrect lubricants can cause premature wear or even damage components, so always consult the manufacturer’s recommendations. -
Ignoring Cycle Time Changes:
A change in cycle time can indicate hidden issues. Monitoring cycle times closely can help you catch early signs of trouble. -
Infrequent Filter Replacements:
Failing to replace filters in cooling and hydraulic systems can lead to clogs and overheating, damaging the machine.
By addressing these common mistakes, manufacturers can significantly extend the life of their plastic injection molding machines and reduce downtime.
Preventive Maintenance Checklist
An effective injection molding maintenance plan includes a comprehensive checklist to maintain all components. This checklist should cover mechanical, hydraulic, and electrical systems to ensure the machine operates smoothly.
-
Hydraulic System Maintenance:
The hydraulic system is vital for machines that use hydraulic power for clamping and injection. Check hydraulic oil levels regularly and replace filters as recommended by the manufacturer. Ensure all hoses and fittings are secure and inspect for leaks. -
Electrical System Checks:
Regularly inspect the electrical components, including wiring and connections. Electrical systems control critical functions, so routine checks prevent malfunctions that could interrupt production. -
Cooling System Maintenance:
Injection molding machines generate a significant amount of heat. Inspect the cooling system and make sure it is functioning correctly. Clean or replace cooling system filters to prevent clogging, which can lead to overheating and machine damage. -
Screw and Barrel Maintenance:
Inspect the screw and barrel for wear, align and tighten any loose parts, and replace worn parts promptly to avoid further damage.
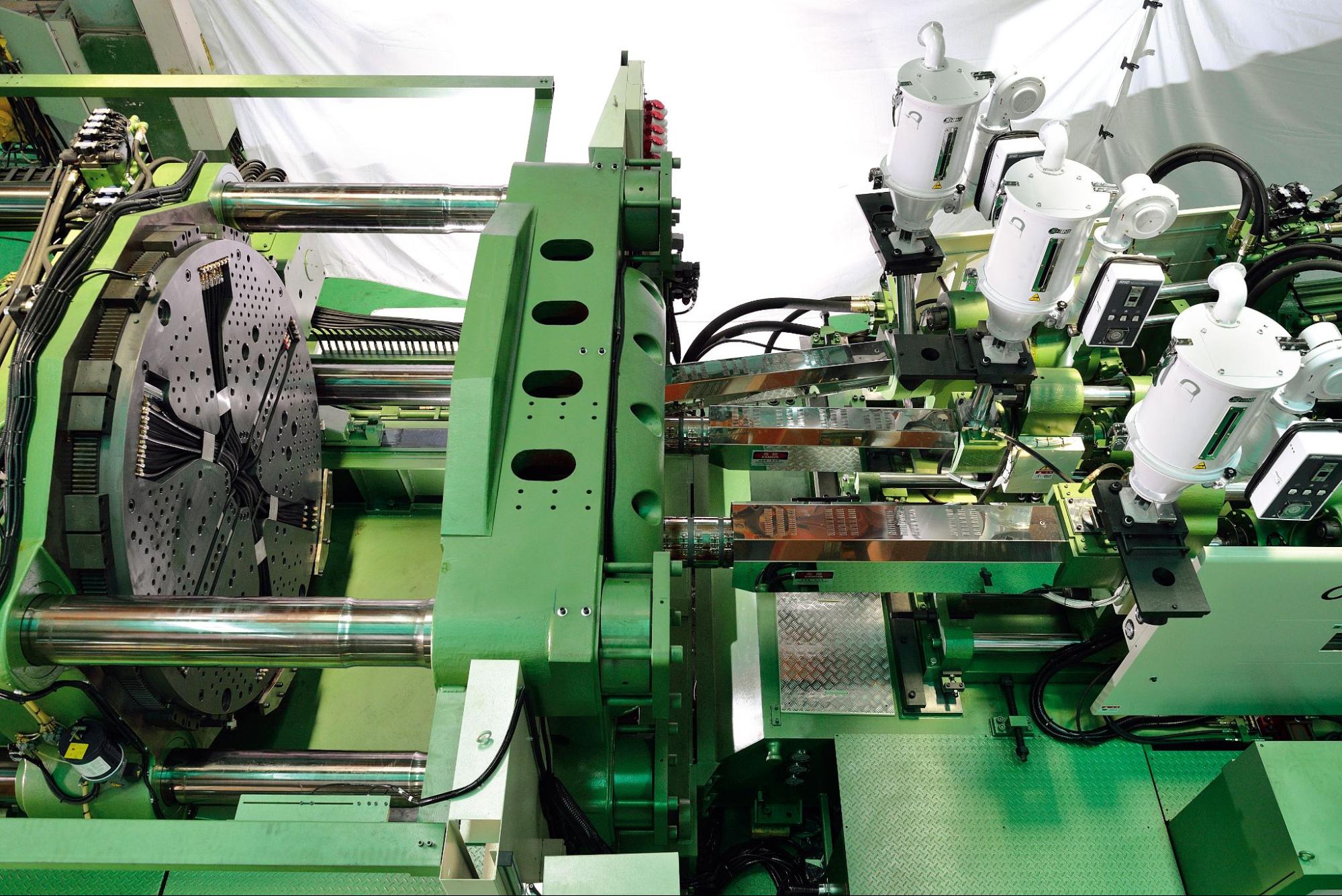
Maximizing Your Machine’s Lifespan with CLF’s Expertise
Maintaining a plastic injection molding machine is an essential investment in the longevity, efficiency, and productivity of your operations. Regular cleaning, lubrication, and monitoring, combined with a well-structured preventive maintenance plan, are key to extending your machine’s lifespan and optimizing production costs. By adopting these practices, manufacturers can achieve high-quality output, minimize downtime, and secure a competitive edge.
For those in the automotive parts, plastic pallet, PET preform, and other industries, CLF stands as an expert in injection molding machine solutions. Not only does CLF provide state-of-the-art machinery, but we also deliver complete solutions that include top-tier after-sales support. Our team is dedicated to guiding you through effective maintenance practices, ensuring smooth operations and outstanding performance. With a proven track record of customer satisfaction globally, CLF is here to help you maximize your investment and achieve consistent, high-quality results. Contact Us Now !
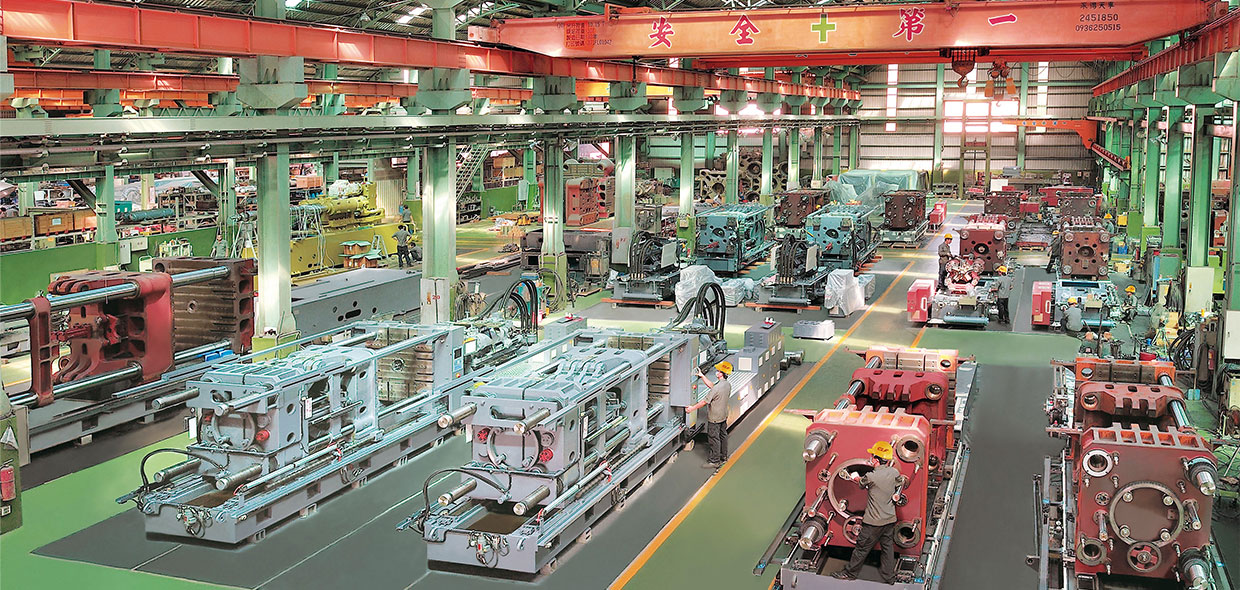