Enhancing Large Furniture Production in Iran: How CLF Injection Molding Machines Delivered Superior Mixing and Consistent Quality
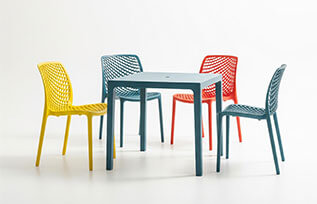
A Leading Iranian Home Goods Manufacturer’s Injection Molding Challenges
In Iran, a prominent manufacturer specializing in plastic home products—including large furniture such as tables and chairs—faced persistent difficulties maintaining consistent product quality. Their production relied heavily on polypropylene (PP) and polyethylene (PE), compounded by a high percentage of recycled materials and masterbatch additives.
These initial circumstances set the stage for significant operational hurdles the team needed to overcome.
Challenges: Overcoming Quality and Efficiency Issues in Injection Molding
The manufacturer’s production team identified several critical challenges:
-
Uneven Material Mixing
: High recycled content and masterbatch usage resulted in inconsistent color dispersion and poor blending. -
Inconsistent Product Quality
: Variations in mixing caused fluctuations in part strength and surface finish, increasing defect rates. -
Demanding Large-Scale Molding Requirements
: Producing large furniture pieces required stable, high-clamping-force machinery to maintain cycle times and part uniformity.
To address these challenges effectively, the company looked to CLF for a proven, customized solution.
Read more : How to Select Large Plastic Injection Machines? 3 Tips
Solution: Customized Injection Molding Machine Configuration for Recycled Material Processing
This Iranian manufacturer has maintained a long-standing partnership with CLF since 2000. Over the years, they have acquired nearly 80 units CLF injection molding machines, progressively upgrading from early-generation models to advanced high-tonnage systems. Their equipment lineup now ranges from compact and versatile TX series machines to powerful 2800TWII models designed for large-scale furniture molding.
In response to their growing reliance on recycled materials and demand for higher consistency, CLF proposed a tailored machine configuration that addressed both mixing challenges and large-part production needs:
- CLF 180TX Series – for smaller molded parts requiring high precision and consistent material feeding
- CLF 2800TWII Series – a robust, high-clamping-force machine ideal for large furniture items
To ensure optimal processing of PP/PE blends with masterbatch and recycled content, CLF implemented:
- A high-shear screw design for enhanced dispersion
- Extended screw L/D ratio for improved melt homogeneity
This project was more than just machine delivery—it was a continuation of CLF’s role as a technical advisor. The deployment included:
- On-site commissioning and fine-tuning for recycled material settings
- Dedicated training to equip operators with the skills for efficient operation
- Long-term technical follow-up to support stable, high-yield production
Through years of collaboration, CLF has not only delivered machines but also evolved with the customer’s production needs, helping them scale from early-stage operations to a modern, sustainable manufacturing model.
Read more : Two-Platen vs. Three-Platen Injection Molding Machines: Which One is Right for You?
Results: Achieving Superior Production Outcomes with CLF Injection Molding Solutions
Following deployment of the CLF injection molding machines, the manufacturer reported significant performance gains:
-
Color Variation Reduction
: Over 80% decrease in color inconsistency across batches. -
Yield Stabilization
: Production yields increased to over 95% consistent first-pass quality. -
Enhanced Efficiency
: The 2800-ton TWII injection molding machine maintained short cycle times while delivering high clamping force for large molds, boosting output by 25%. -
Improved Part Quality
: Surface finish and strength metrics exceeded customer standards, reducing post-production rework.
Beyond these impressive results, the customer shared their experience working with CLF.
How CLF Made a Difference
“Thanks to CLF’s injection molding solutions, we’ve transformed our production capabilities. The customized screw design resolved our quality issues, and the powerful machines enabled us to produce large furniture parts efficiently. Their professional support and technical expertise have been invaluable in achieving stable, high-yield operations.”
Their feedback underscores the value of choosing the right injection molding partner.
Ready to Transform Your Injection Molding Operations?
Ready to enhance your injection molding operations? Contact the CLF team today to explore customized solutions that help you produce high-quality products with maximum efficiency.