Two-Platen vs. Three-Platen Injection Molding Machines: Which One is Right for You?
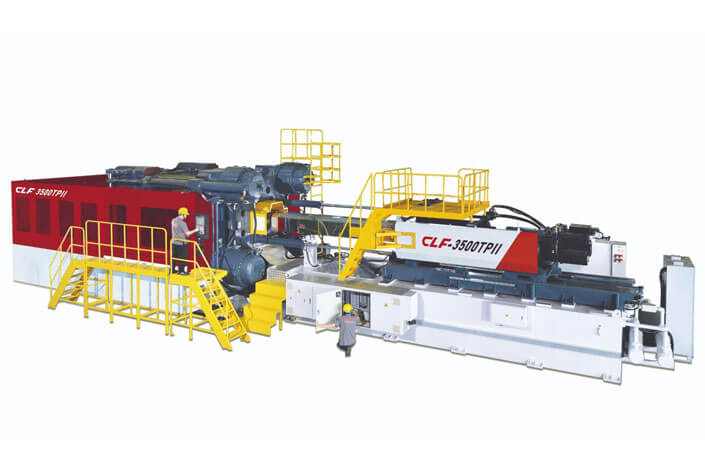
Injection molding is a widely used manufacturing process for producing plastic parts and products. Within this field, different injection molding machine designs cater to various production needs. Two-platen and three-platen injection molding machines are two common configurations with distinct characteristics, each offering unique advantages for specific applications.
Two-Platen Injection Molding Machines
A two-platen injection molding machine features two large platens that are used for clamping the mold. This design offers several advantages:
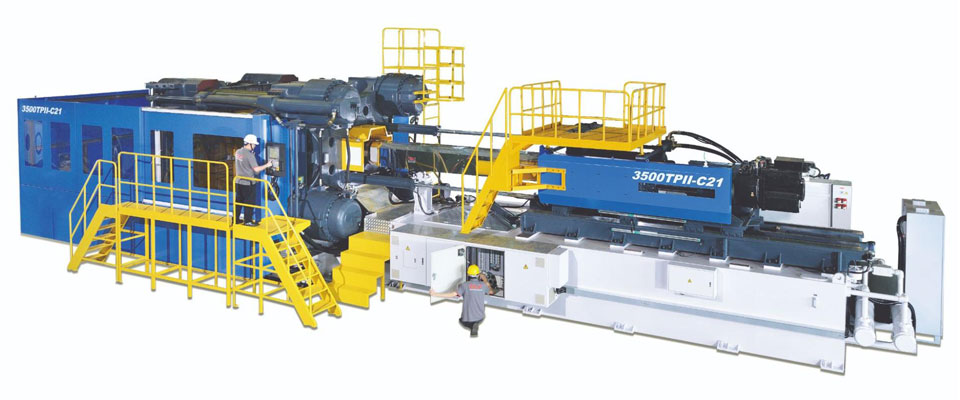
Space Efficiency
Two-platen injection molding machines are generally more space-efficient than outward toggle type machines. This is because two-platen machines use a direct hydraulic locking mechanism, which eliminates the need for mechanical linkages. Mechanical linkages, which are required for outward toggle type machines, can add significant length to the machine. As a result, two-platen machines can be up to 15-20% shorter than outward toggle type machines, providing a significant space savings for manufacturers.
High Stability, High Precision and Good Maintenance
Two-platen machines offer increased platen stability during the molding process. This enhanced stability can result in improved part quality, better dimensional accuracy, and reduced variations in finished products. Besides, comparing to toggle-type machines, without the wear and tear of toggle and oil pollution, it is easier to maintain.
Large Mold Capacity and Improved Accessibility
The spacious design between the platens allows for larger molds, enabling the production of bigger parts or multiple-cavity molds. Besides, with more space between the platens, two-platen machines provide better access to the mold area. This can simplify mold changes, maintenance, and troubleshooting.
Applications
With a larger mold space and shortened length of machine size, the two-platen injection molding machine is usually used as a medium or large-sized plastic parts molding equipment. Especially for applications that require space efficiency, high stability, and precision, such as large auto parts, large households or logistic products.
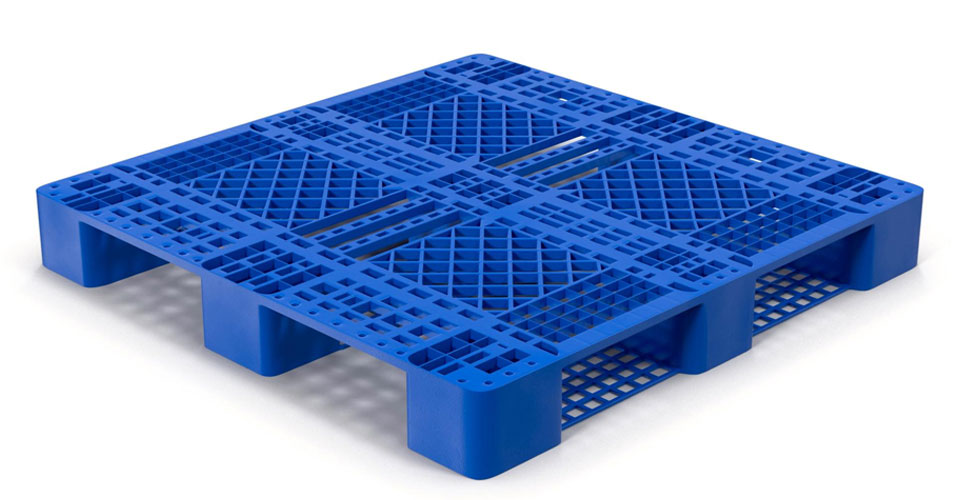
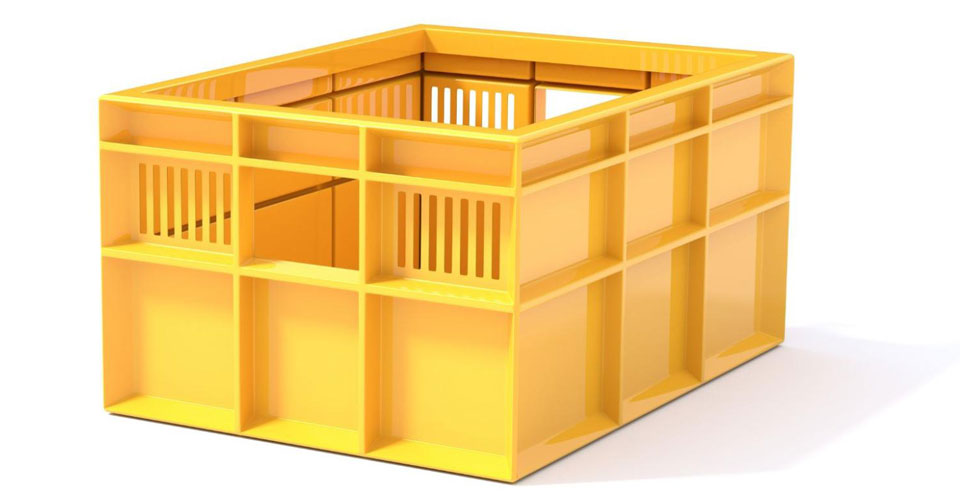
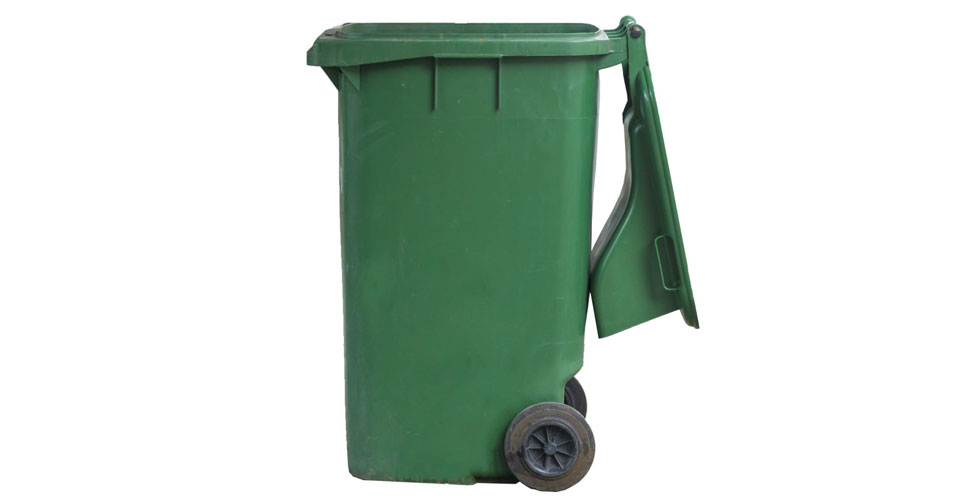
Learn more: Top 3 Advantages of Plastic Pallet Injection Molding machine
Three-Platen Injection Molding Machines
A three-platen injection molding machine machine, also called toggle-type machine, has a toggle mechanism that connects the moving platen to the stationary platen. As the machine closes, this toggle mechanism locks the mold. Here are some characteristics of toggle-type machines:
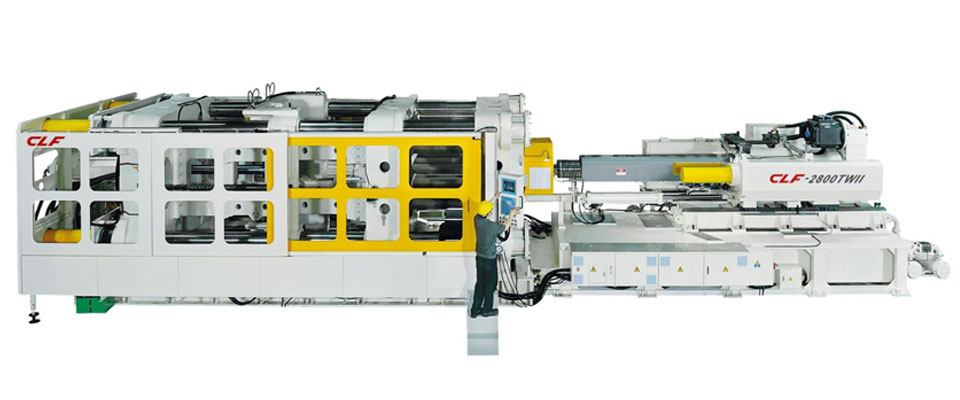
Short Cycle Time
Three-platen machines, with toggle mechanisms, allow for quick mold opening and closing, resulting in shorter cycle times compared to some other machine designs. This also makes it well-suited for high-volume production where cycle time reduction is crucial. Besides, enabling efficient and precise filling of molds, which can be advantageous for producing parts with intricate details and thin walls.
Convenient Mold Handling
The three-platen structure allows independent movement of the middle platen and the bottom platen. This facilitates easier mold installation, operation, and maintenance. Furthermore, three-platen machines are suitable for molds that require multiple parts, including those with complex shapes or hollow structures.
Applications
Three-platen machines are well-suited for applications that require high speed, short cycle time or high production. Especially for small or thin plastic products, such as electronic parts, small auto parts or PET containers.
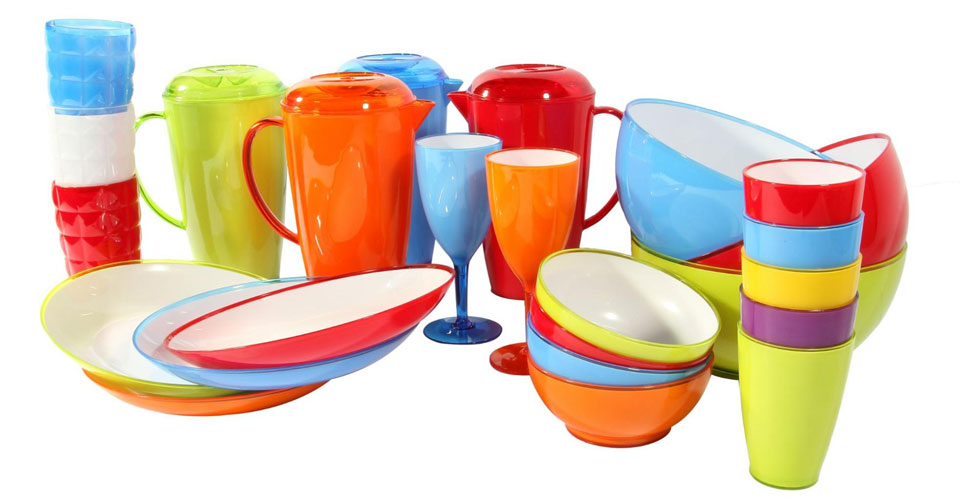
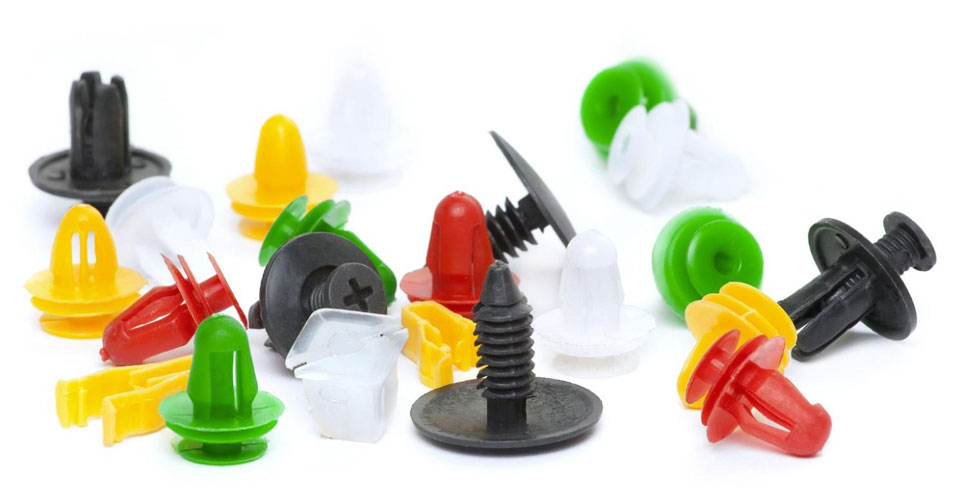
Comparison of Two-Platen and Three-Platen Injection Molding Machines
The Final Selection
In summary, two-platen and three-platen injection molding machines each offer unique advantages. Selecting the appropriate machine is crucial to optimize production efficiency and meet the needs of a particular application. The choice between two-platen and three-platen injection molding machines depends on the specific production requirements. Key factors to consider include product size, complexity, required clamping force, energy efficiency goals, cycle time, available space, and budget constraints. Therefore, before you purchase the equipment, make sure that you figure out your business needs and the applications of two kinds of machine design.
At CLF, we have been providing injection molding turnkey solutions for nearly 50 years. We specialize in building large injection molding machine that last for decades. Our injection molding machines are used for a variety of industries, such as plastic pallets, car bumper, PET preform, automotive parts, automotive lighting, etc. If you would like to learn more about how we can design and build a large injection molding machine for your project, please contact us today!